Ultra-fine lithium powder is a key lithium compound and an essential factor in the development and revenue generation of the lithium battery industry.
In the lithium battery industry, we are constantly pursuing innovations in battery technology to meet the demand for higher performance, larger capacity, longer life, faster charging speed and lighter weight batteries. In order to achieve these goals, battery manufacturers must ensure that the lithium compounds used meet strict particle size distribution standards.
The application of ultra-fine lithium powder, due to its unique physical properties, plays a key role in improving battery performance. This article will introduce the lithium powder grinding process in detail and explore how to optimize battery performance by precisely controlling the particle size distribution of lithium powder.
Common Problems in Battery Material Crushing
The crushed material has many impurities, and the battery self-discharge capacity is reduced.
Low production efficiency, excessive energy consumption.
Difficult to control water intake, poor safety.
Equipment operation is unstable, and the quality of finished products is uneven.
Dust is difficult to control, and low battery voltage problems are common.
★ Clirik has designed a set of efficient and low-cost ultrafine lithium powder processing technology with advanced crushing and grinding equipment, successfully solving the above problems.
Grinding process of ultra-fine lithium powder
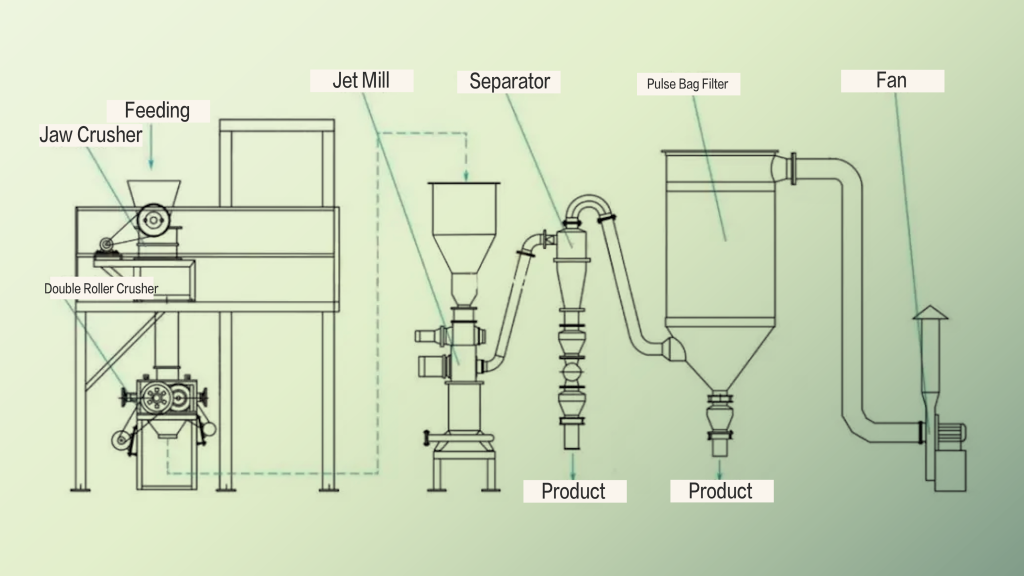
Ultra-fine lithium powder processing equipment
Jaw Crusher
The Jaw Crusher uses a dynamic extrusion technique for crushing. Powered by a motor, it moves the movable jaw in a vertical motion via a belt and pulley system. The continuous rotation of the motor makes the jaw compress and release materials periodically, which aids in the batch production process.
Advantages include a high crushing ratio, consistent particle size, straightforward structure, dependable performance, and ease of operation and maintenance.
Double Roller Crusher
The Double Roller Crusher, powered by a motor, drives the rollers to rotate in opposite directions. As materials are fed into the machine through the inlet, they are compressed by the rolling action of the rollers. Consequently, they are then discharged as crushed products from the bottom of the frame.
Advantages include a high crushing ratio with low noise levels, overload protection for reliability, high efficiency, and the production of uniformly sized particles.
Jet Crusher
The Jet Crusher utilizes high-velocity airflow as both power and carrier, transforming the compressed air stream into kinetic energy through the nozzle within the grinding chamber.
Advantages include low energy consumption, high fineness, straightforward structure, and uniform particle size of the end product.