Spring Cone Crusher
High-efficiency Hydraulic Cone Crusher is a world-level cone crusher introduced with the up-to-the-minute technology of Germany.It is the most ideal equipment for large stone crushing factory and mining industry.
Output size:
<64mm
Power:
75-315kw
Capacity:
27-1400t/h
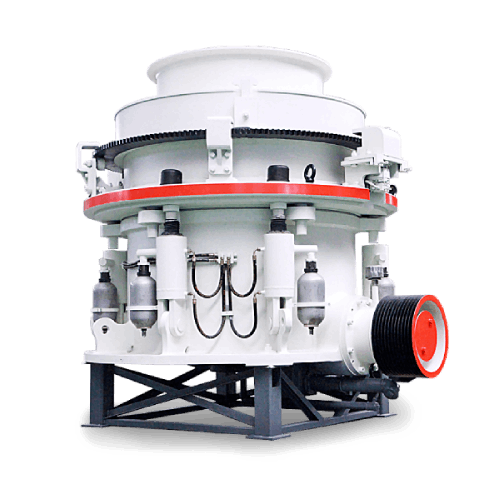
Technical Advantages
Spring cone crushers are made to last, with an easy-to-use design. Made from strong American steel, they’re designed for many years of dependable work.
Their frames and components are constructed with a keen attention to detail by experienced craftsmen, ensuring ruggedness and durability in every unit.
They are easy to maintain, with accessible components that simplify routine checks and part replacements.
The simplicity of the design also means that operators can quickly learn how to manage the crusher, reducing the need for extensive training and allowing for efficient operation.
Spring cone crushers utilize a laminating crushing technique, which ensures that materials are crushed into smaller sizes with better shape and consistency.
This advanced technology leads to improved output quality, making it suitable for applications that demand fine and uniform particle sizes.
These crushers cost little to run and can do many jobs. A kit lets them get new features that make them work better and smarter, saving money for all sorts of crushing tasks.
A great thing about spring cone crushers is that you can choose from different crushing spaces inside. You can set it up for big, medium, or small crushing to get just what you need.




Working Principle
The cone crusher initiates its operation with the motor driving the eccentric sleeve through a series of connected components, including the triangle belt, large belt wheel, rotating shaft, small bevel gear, and large bevel gear.
This sequence of mechanical linkages ensures the activation of the crushing process.
As the eccentric sleeve rotates, it imparts an oscillating motion to the broken cone axis line, causing the crushing wall surface to alternately approach and recede from the surface of the rolling mortar wall.
This creates a dynamic environment within the crushing chamber.
Inside the crushing chamber, the material is subjected to continuous forces as the moving cone, driven by the oscillating motion, applies impact, pressure, and bending to the material.
This process is repeated several times, effectively breaking down the material.
After undergoing multiple cycles of compression, impact, and flexure, the material reaches the desired particle size and is discharged through the lower portion of the crusher.
Parameters
Model | Cone Diameter(mm) | Chamber | Close Feeder Side (mm) | Open Feeder Side (mm) | Output Size (mm) | Capacity (ton/hour) | Rotor Speed (r.p.m) | Power (kw) | Weight (ton) | Dimension (mm) |
CS75B | 900(3‘) | M | 83 | 102 | 9-22 | 45-91 | 580 | 75 | 15 | 2821*1880*2164 |
CS75B | 900(3‘) | L | 159 | 175 | 13-38 | 59-163 | 580 | 75 | 15 | 2821*1880*2164 |
CS75D | 914(3‘) | S | 13 | 41 | 3-13 | 27-90 | 580 | 75 | 15 | 2821*1880*2410 |
CS75D | 914(3‘) | M | 33 | 60 | 3-16 | 27-100 | 580 | 75 | 15 | 2821*1880*2410 |
CS75D | 914(3‘) | L | 51 | 76 | 6-19 | 65-140 | 580 | 75 | 15 | 2821*1880*2410 |
CS160B | 1295(4‘) | S | 109 | 137 | 13-31 | 109-181 | 485 | 185 | 27 | 2800*2342*2668 |
CS160B | 1295(4‘) | M | 188 | 210 | 16-31 | 132-253 | 485 | 185 | 27 | 2800*2342*2668 |
CS160B | 1295(4‘) | L | 216 | 241 | 19-51 | 172-349 | 485 | 185 | 27 | 2800*2342*2668 |
CS240B | 1650(4‘) | S | 188 | 209 | 16-38 | 181-327 | 485 | 240 | 55 | 3911*2870*3771 |
CS240B | 1650(4‘) | M | 213 | 241 | 22-51 | 258-417 | 485 | 240 | 55 | 3911*2870*3771 |
CS240B | 1650(4‘) | L | 241 | 268 | 25-64 | 299-635 | 485 | 240 | 55 | 3911*2870*3771 |
CS400B | 2134(7‘) | S | 253 | 278 | 19-38 | 381-726 | 435 | 315 | 110 | 4613*3251*4732 |
CS400B | 2134(7‘) | M | 303 | 334 | 25-51 | 608-998 | 435 | 315 | 110 | 4613*3251*4732 |
CS400B | 2134(7‘) | L | 334 | 369 | 31-64 | 870-1400 | 435 | 315 | 110 | 4613*3251*4732 |