Brief Introduction
CLRM enhanced roller mill is suitable for processing various non-flammable and non-explosive mineral materials with Moh’s hardness less than 6 and humidity less than 6%.
Scope and Application
It is widely used in the metallurgical field, construction, chemical industry, mining, highway construction, etc.
The particle size of the finished powder size can be adjusted between 80 and 500 mesh. Examples of processed materials include quartz, feldspar, barite, calcite carbonate, limestone, talc, ceramics, iron ore, emery, bauxite, phosphate rock, coal and other materials, a total of about 400 materials.
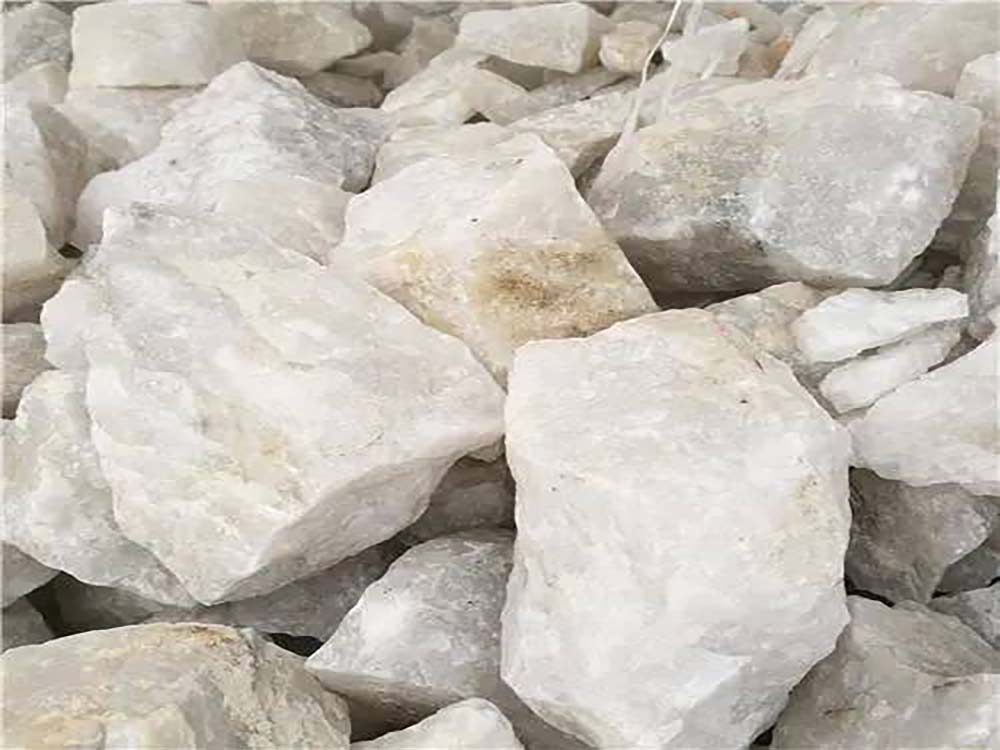
quartz
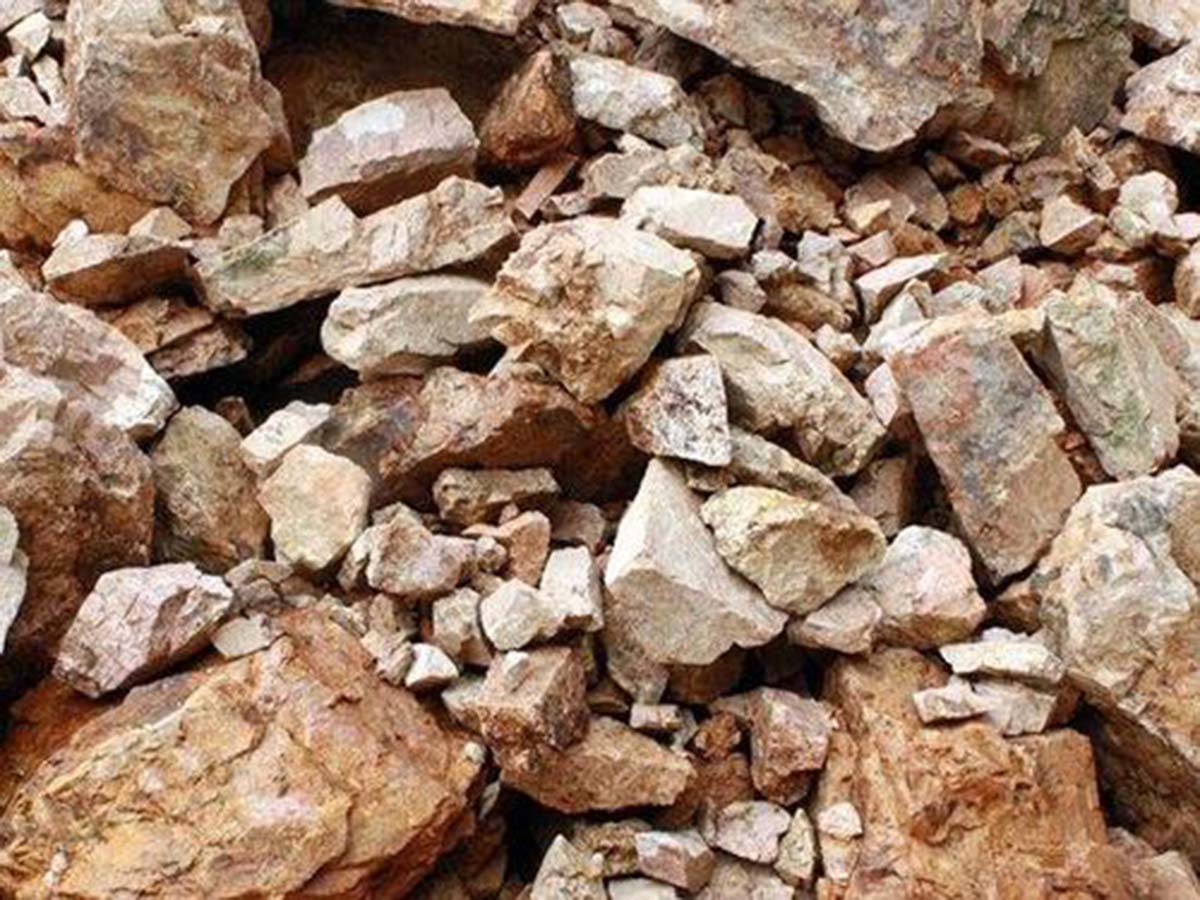
feldspar
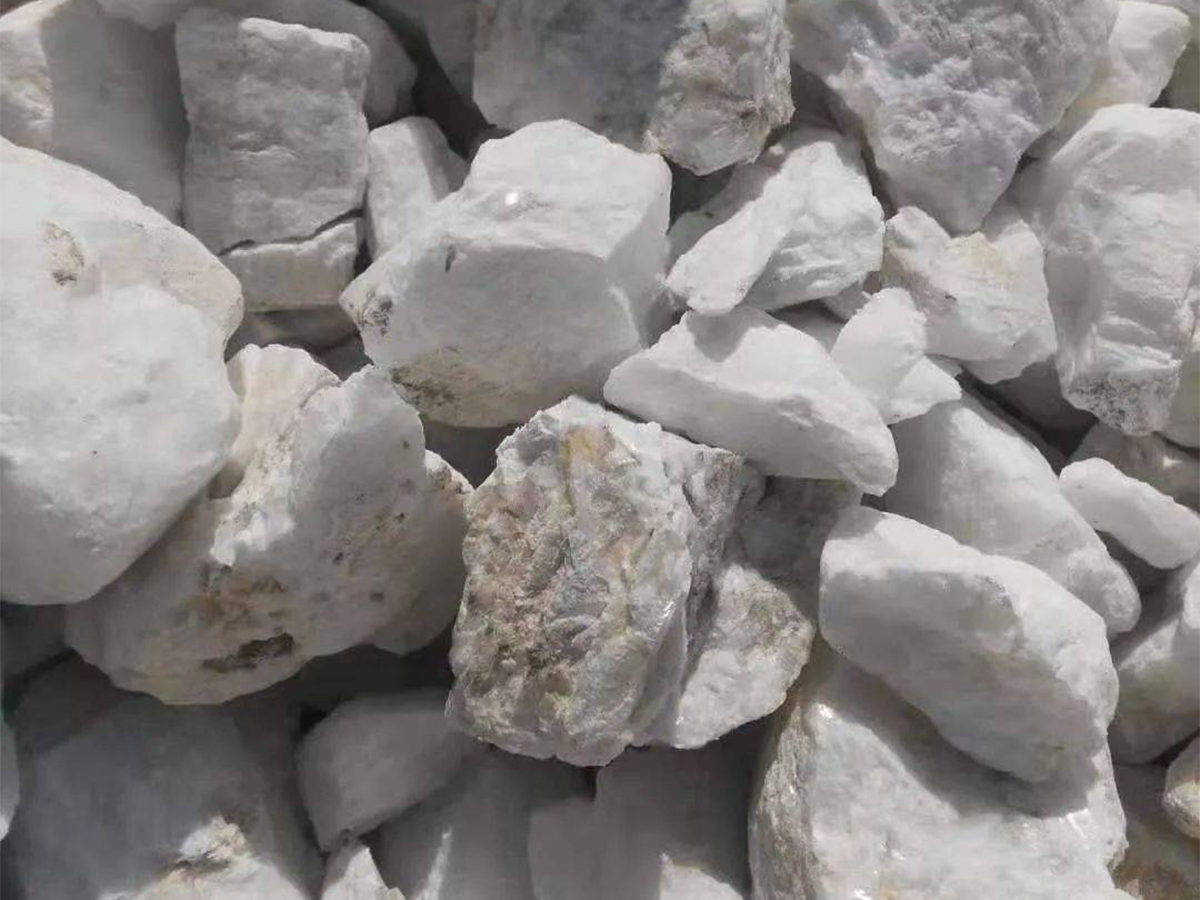
barite
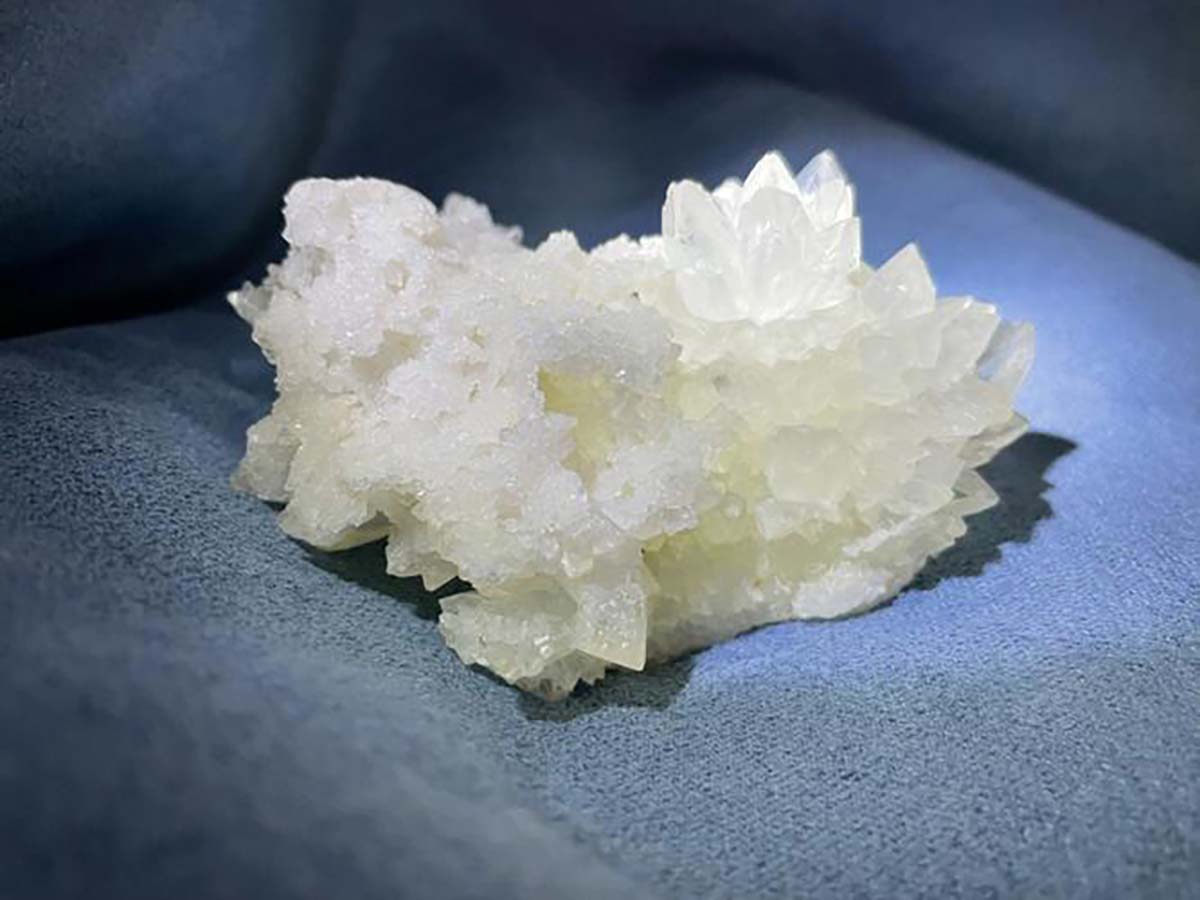
calcite
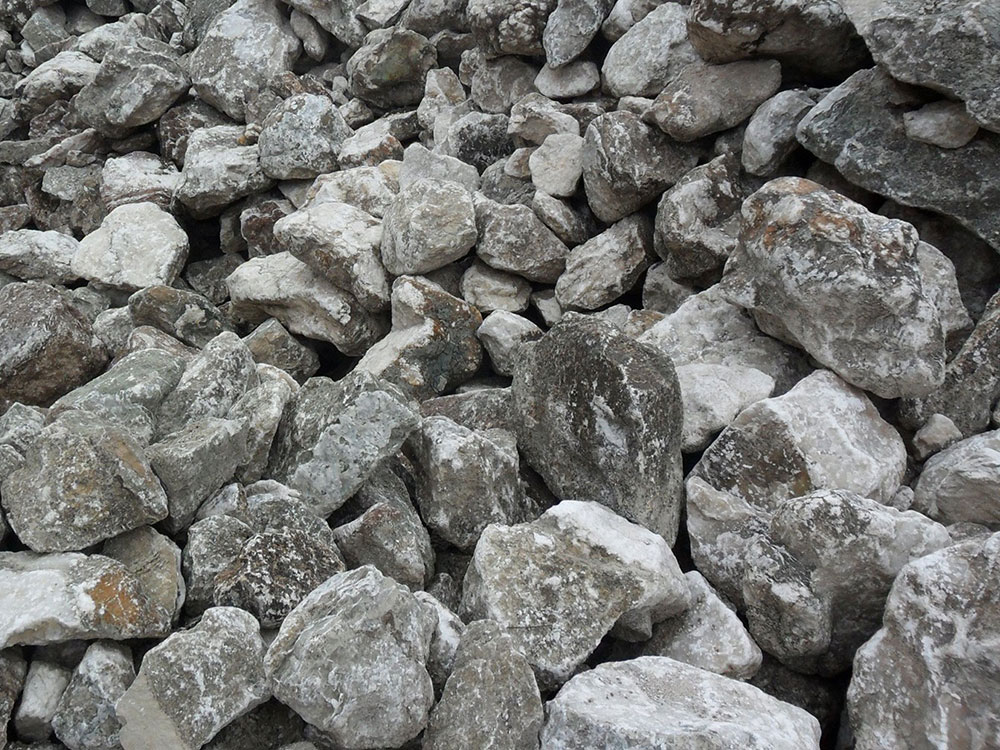
limestone
Production Line Composition
The standard configuration of CLRM enhanced roller mill consists of main machine, reducer, powder classifier, cyclone powder collector, vacuum cleaner, blower, electrical cabinet and pipeline. Optional accessories include crushers, bucket elevators, and feeders.
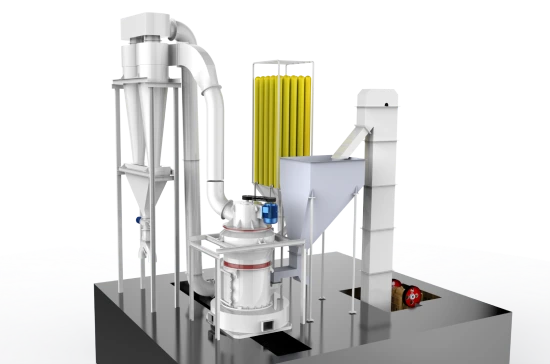
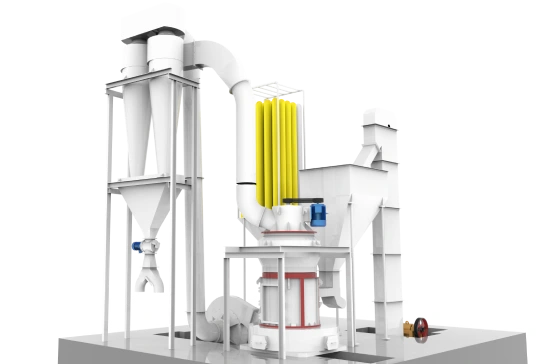
Working Principle
● The aniseed is crushed to the required particle size by the jaw crusher, and then transported to the hopper by the bucket elevator, and is evenly and continuously fed to the host machine for grinding through the vibrating feeder.
● The ground powder is transported from the blower to the classifier by air flow, and the particles that meet the fineness enter the cyclone collector through the pipe, where they are separated and collected. They are discharged at the discharge valve and become the finished product.
● The airflow is drawn to the blower through the return tube at the top of the cyclone collector. The entire air flow system is a sealed cycle and circulates under positive and negative air pressure.
Advantages
Compared with the previous mill, the grinding pressure has increased by 10% and the grinding area has increased by 15 -20%. The drum layout is optimized and sufficient grinding space is added.
Triple damping to resist vibration transmission in the main unit base, volute airflow house, unit body, and grinding part. Ensures stable grinding conditions.
Equipped with a new cage impeller, the speed can be adjusted freely through VFD, expanding the output size range to 80-500 mesh.
Technical Parameters
Model | Roller Qty(pcs) | Roller Size(mm) | Ring External Dia(mm) | Ring Height(mm) | Main Shaft Speed(r/min) | Feeding Size(mm) | Finished fineness (Mesh) | Motor(kw) | Capacity(t/h) |
CLRM9720 | 3-4 | Φ320*200 | 1077 | 200 | 145 | <20 | 80-500 | 45*15*37 | 1-7 |
CLRM1280 | 3 | Φ370*240 | 1280 | 240 | 125 | <20 | 80-400 | 75*15*55 | 2-12 |
CLRM1300 | 4 | Φ410*280 | 1390 | 280 | 112 | <20 | 80-400 | 110*22*90 | 3-15 |
CLRM1620 | 4 | Φ450*300 | 1620 | 300 | 102 | <20 | 80-400 | 160*30*132 | 5-20 |
CLRM1700A | 4 | Φ510*300 | 1700 | 300 | 102 | <30 | 80-325 | 185*37*160 | 6-25 |
CLRM1720 | 4 | Φ510*300 | 1850 | 300 | 92 | <35 | 80-325 | 250*45*185 | 6-25 |
CLRM1900A | 4 | Φ600*300 | 1900 | 300 | 92 | <35 | 80-325 | 250*45*220 | 8-32 |
CLRM2150 | 4 | Φ600*300 | 2150 | 300 | 85 | <35 | 80-325 | 315*45*280 | 12-35 |
Things to note when working with Raymond mill
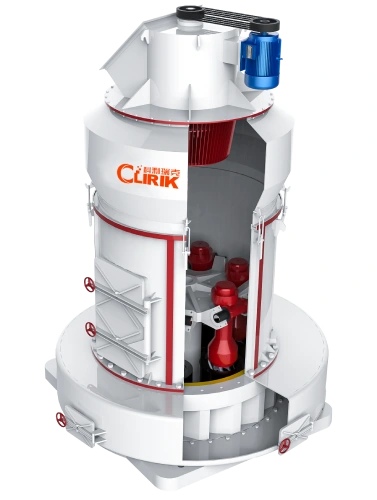
Supervision and Training for Professional Staff
First of all, professional staff should be responsible for supervising the grinding mill during use. Equipment operators must have certain relevant technical levels. Before installing the grinding mill, the operators must receive necessary technical training so that they can understand the principle and performance of the grinding mill and be familiar with the operating procedures, so as to avoid being unable to solve the problem in time when a fault occurs.
Safety and Maintenance Protocols
Secondly, in order for the grinding mill to work normally, relevant safety operating instructions should be formulated to ensure the long-term safe operation of the equipment. At the same time, the equipment must be equipped with necessary maintenance tools, grease and corresponding accessories.
Regular Inspection and Replacement of Wear Parts
The grinding mill should be inspected regularly during use. At the same time, attention should be paid to the maintenance of wearing parts such as grinding rollers, grinding rings, blades, etc. If they are worn, they should be replaced immediately to avoid causing greater damage.