CLUM series ultrafine vertical roller mill
High-efficient multi-rotor concentrator, the finished product has a wide range of particle sizes, the 2μm powder content can reach up to 70%.
Feeding size:
<10mm
Discharging size:
400-3000mesh
Capacity:
1-20t/h
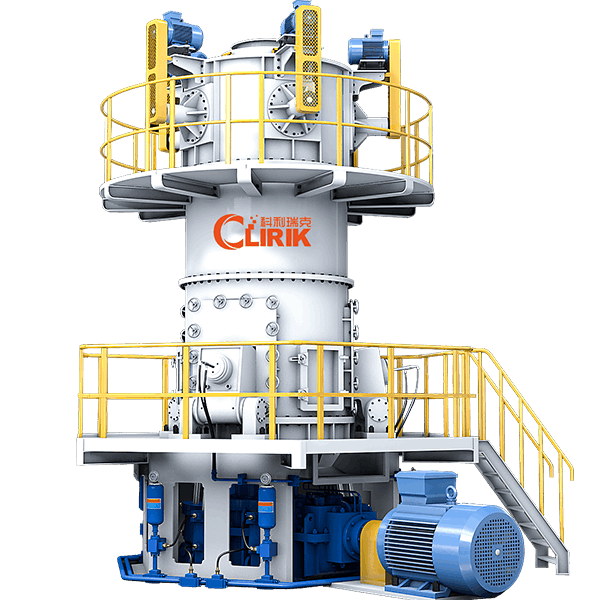
Brief introduction
CLUM series of ultra-fine vertical mills are designed and developed by CLIRIK based on years of experience in grinding production and based on ultra-fine grinding and powder selection technologies from Taiwan and Germany. It is a new type of ultra-fine grinding equipment that integrates grinding, classification, powder collection, conveying and other functions.
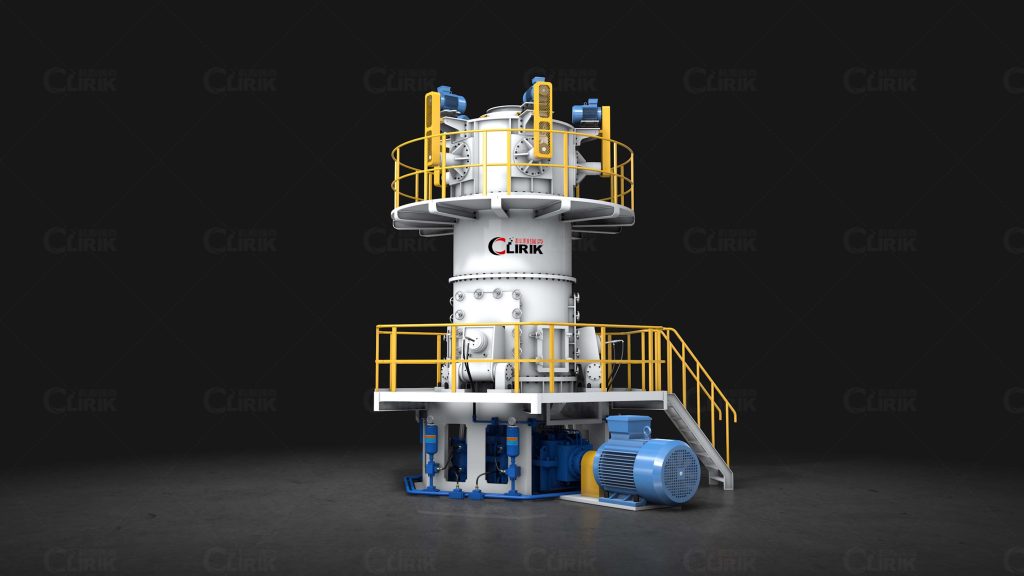
Scope and Application
CLUM series ultra-fine vertical mill is a medium-to-high-end special raw material processing equipment for plastic masterbatching, PVC materials, artificial granite, cables, non-woven fabrics and other industries.
Mainly used for ultra-fine grinding of calcite, marble, limestone, talc, dolomite, heavy stone, kaolin, wollastonite, gypsum, feldspar, pyrophyllite and other non-metallic minerals.
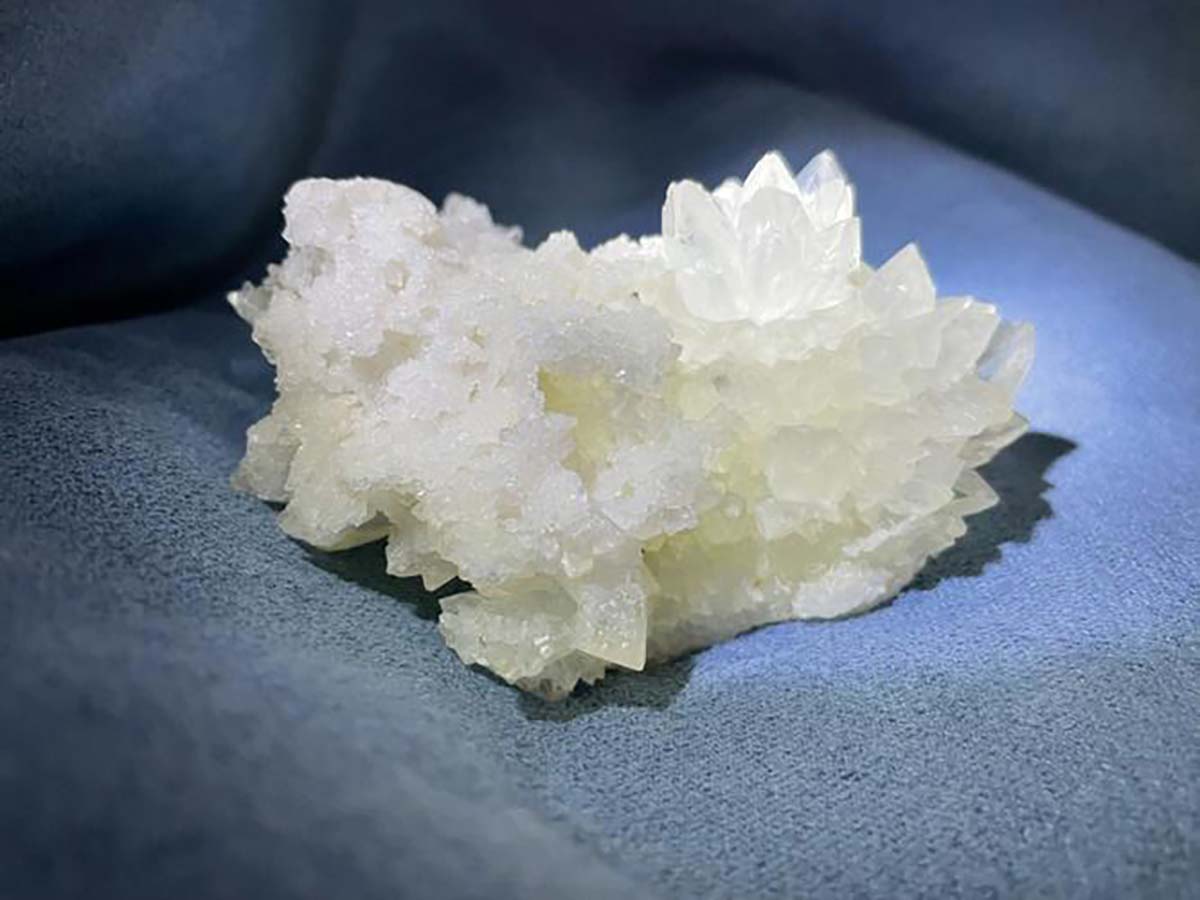
calcite
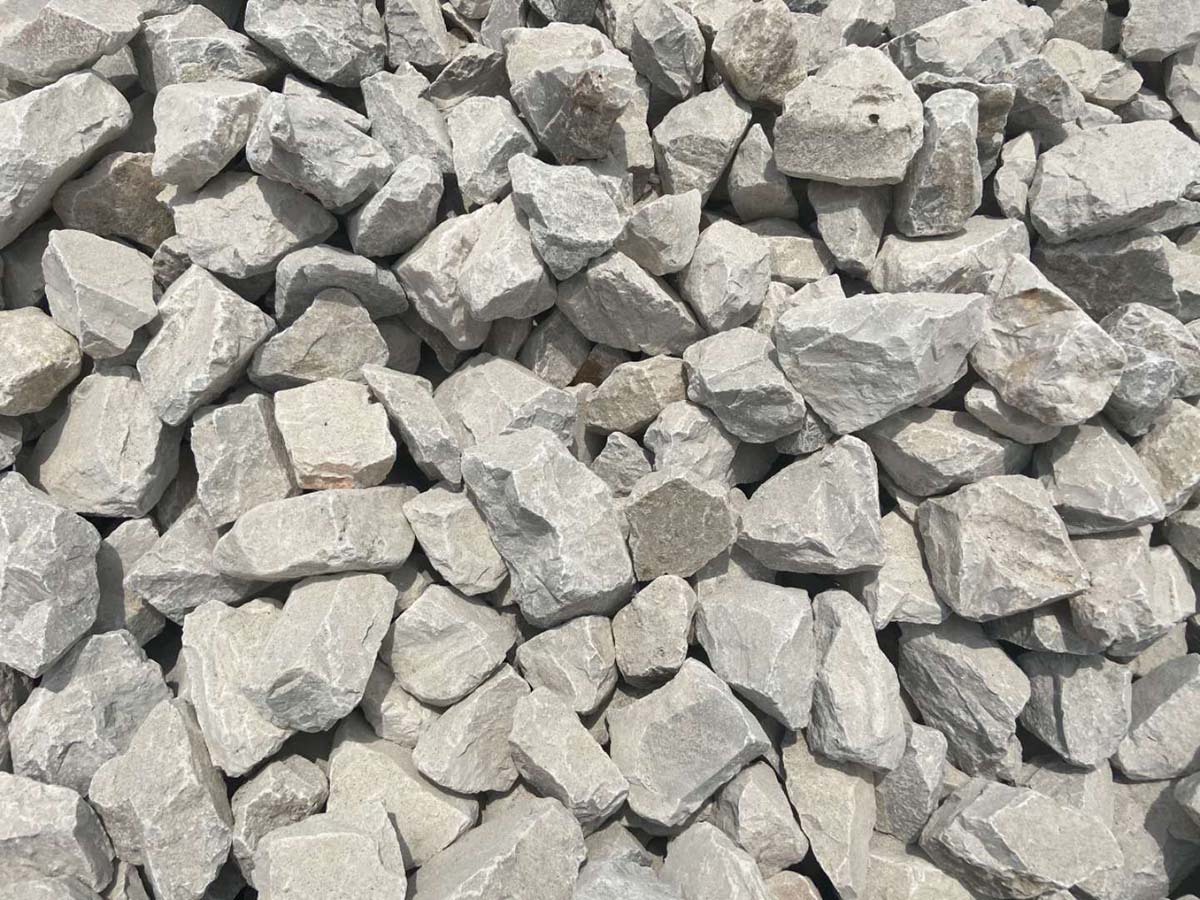
marble
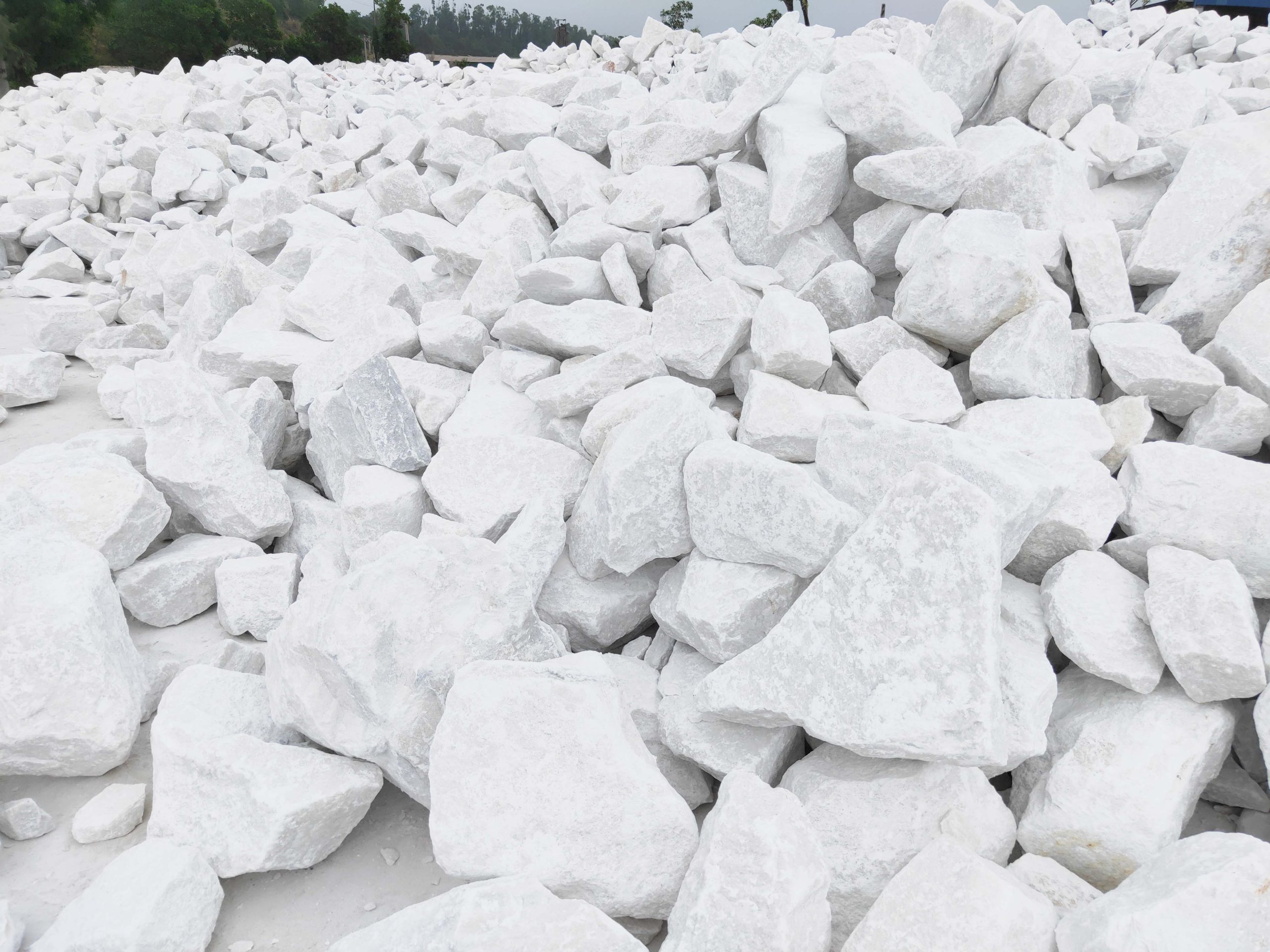
talc
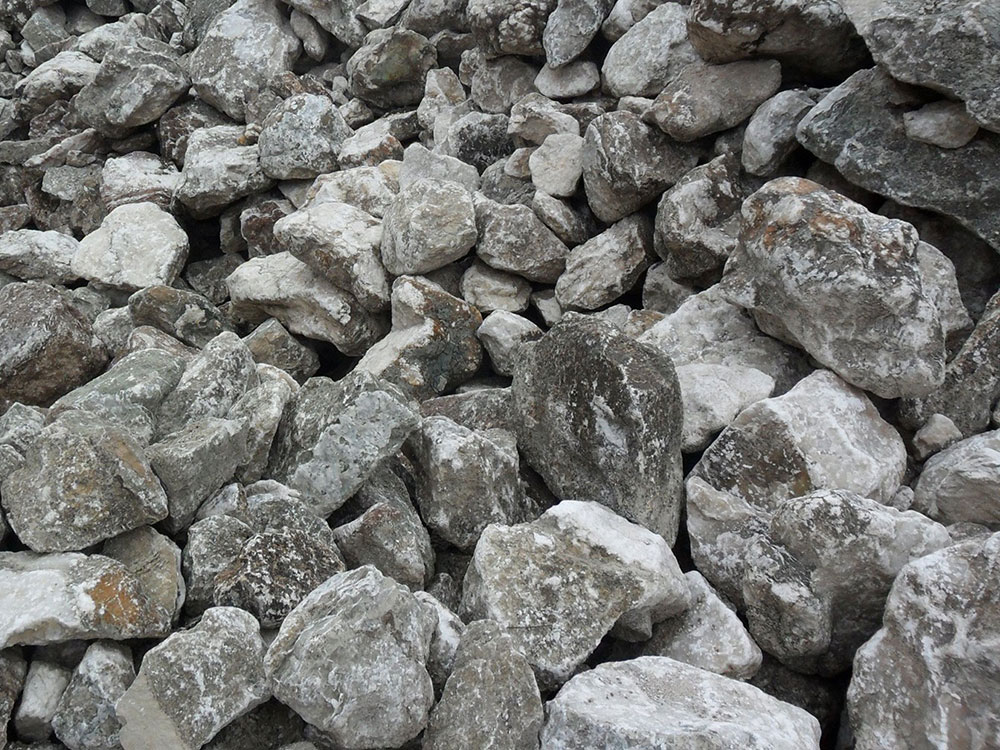
limestone
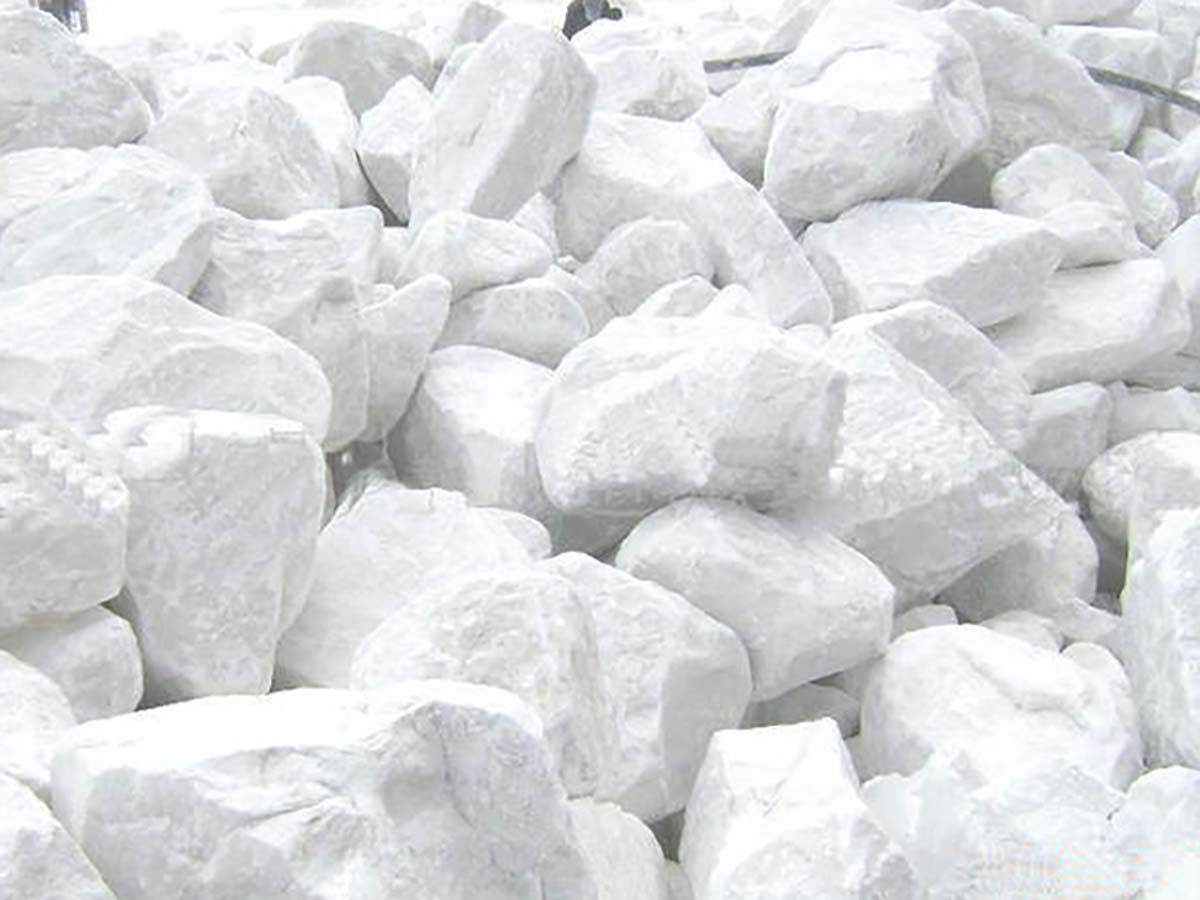
dolomite
CLUM series ultra-fine vertical mill can be widely used in chemical industry, metallurgy, non-metallic minerals and other industries. Especially in the field of ultra-fine grinding processing of white non-metallic minerals, it has excellent performance and can provide high-quality fillers and additives for paper-making, coatings, plastics, rubber, PVC, ink and other industries.
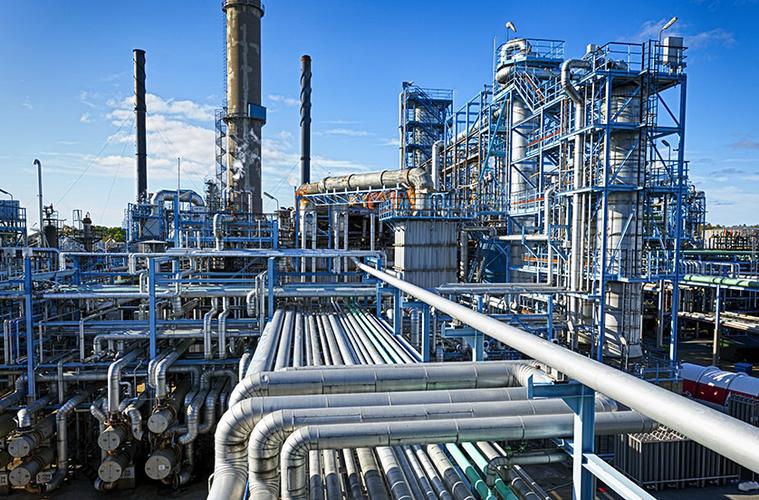
chemical
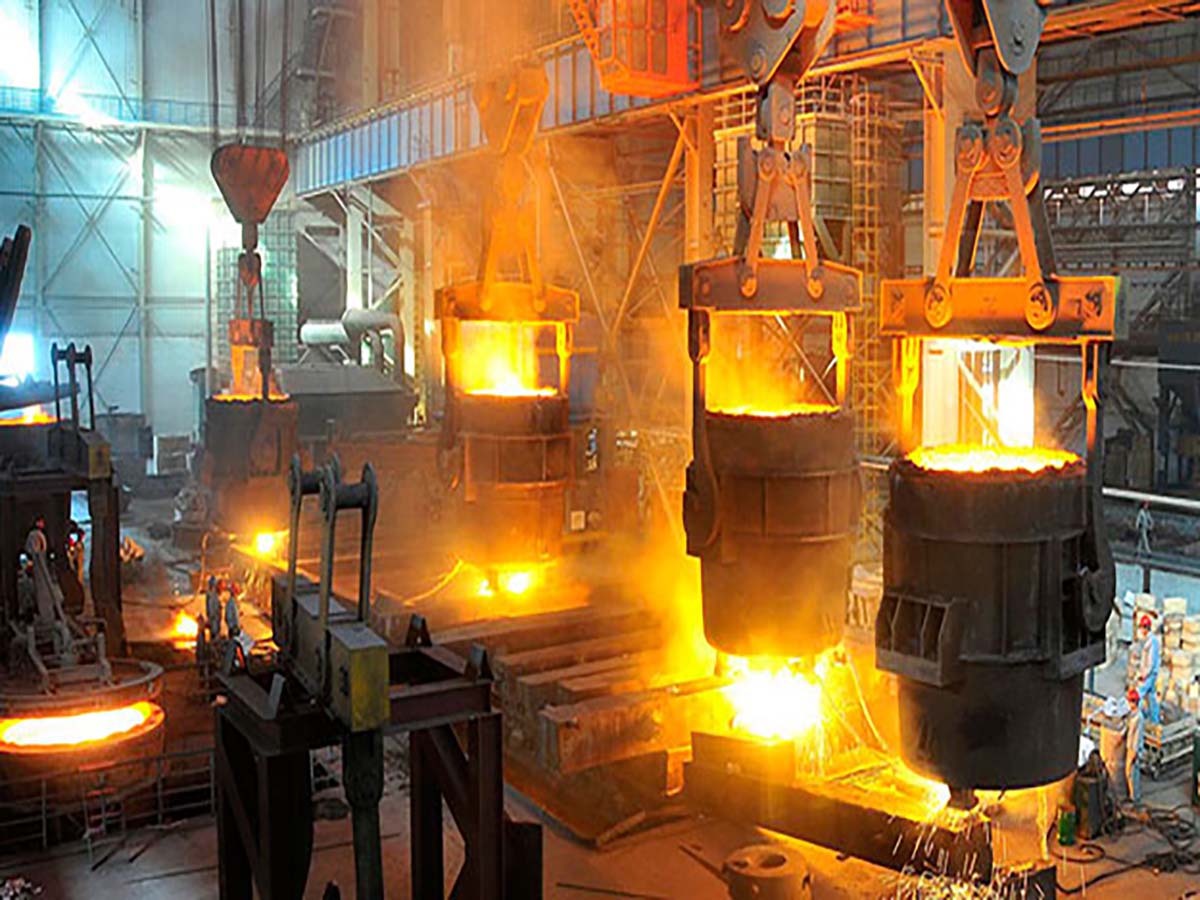
metallurgy
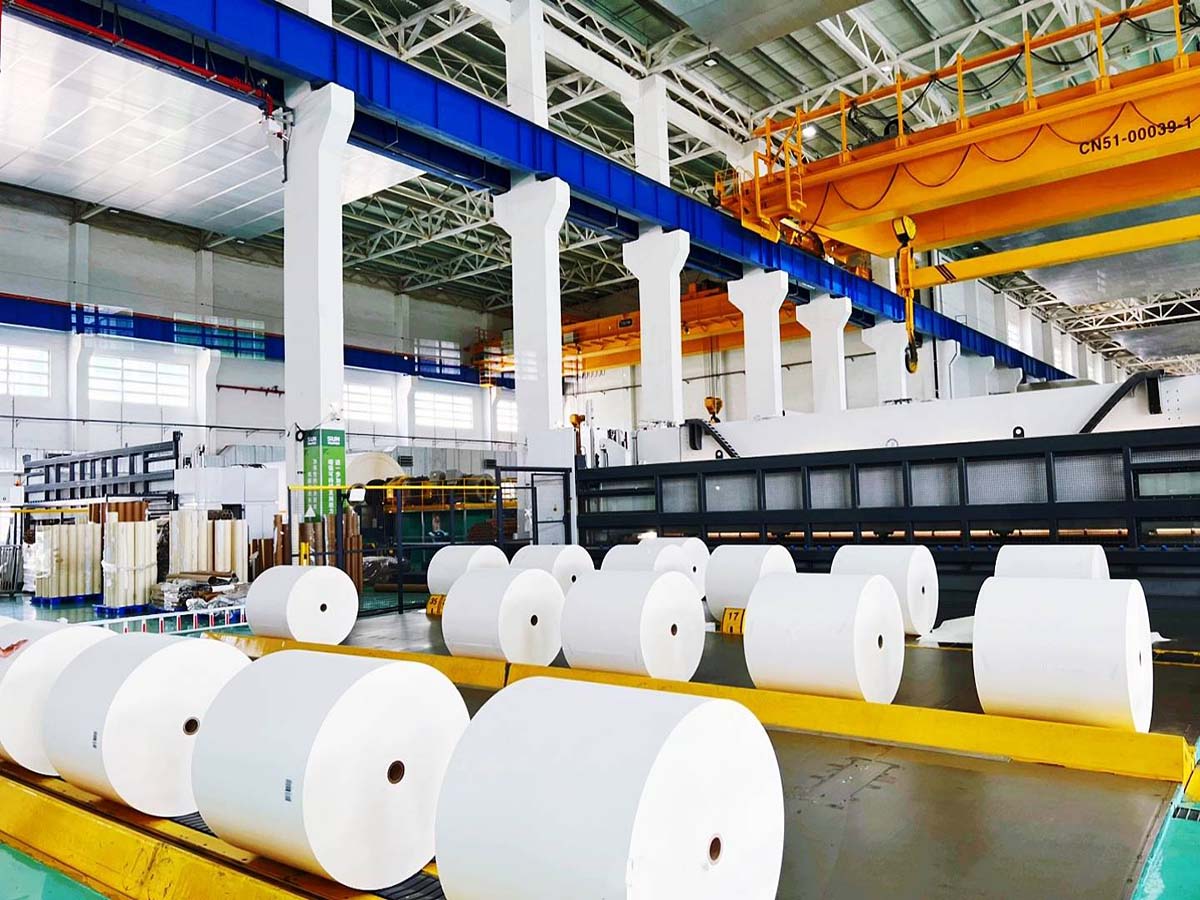
paper-making
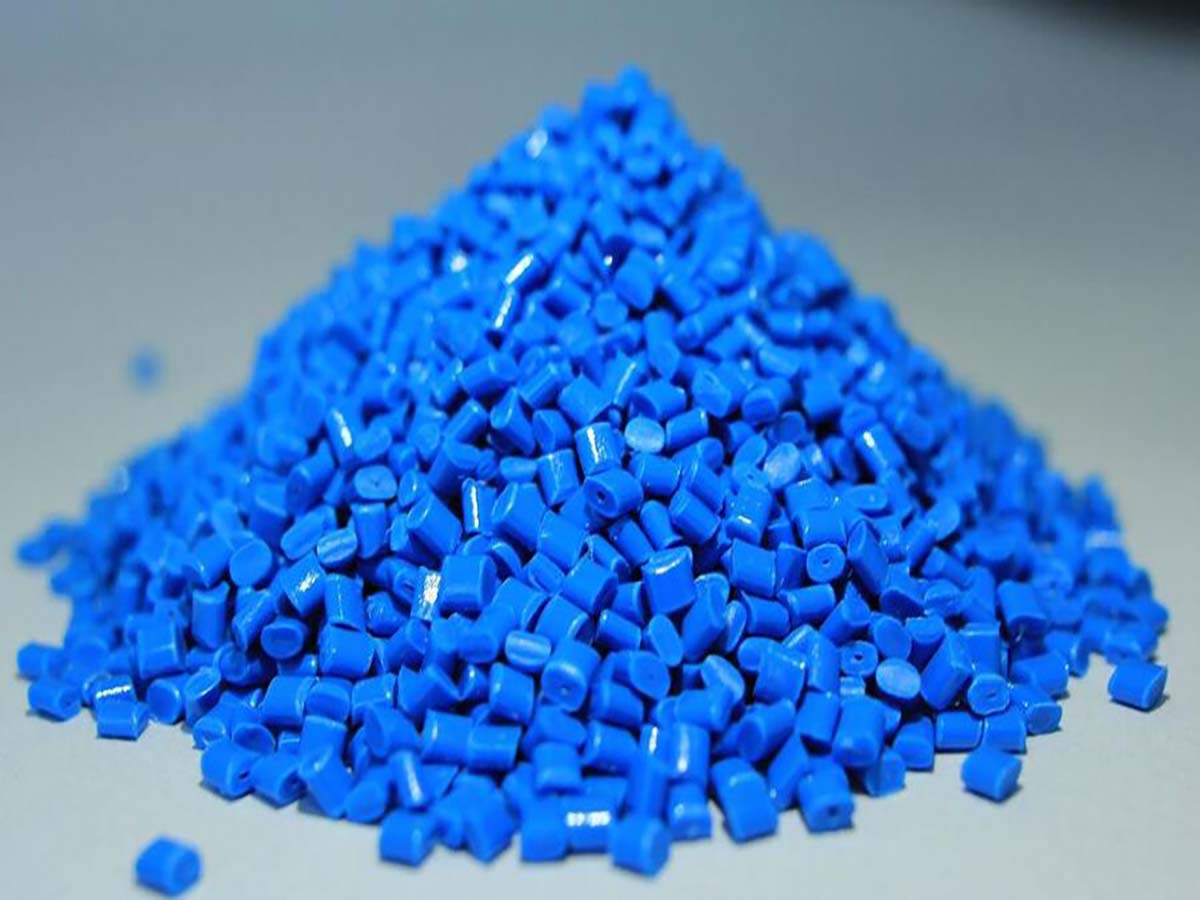
plastics
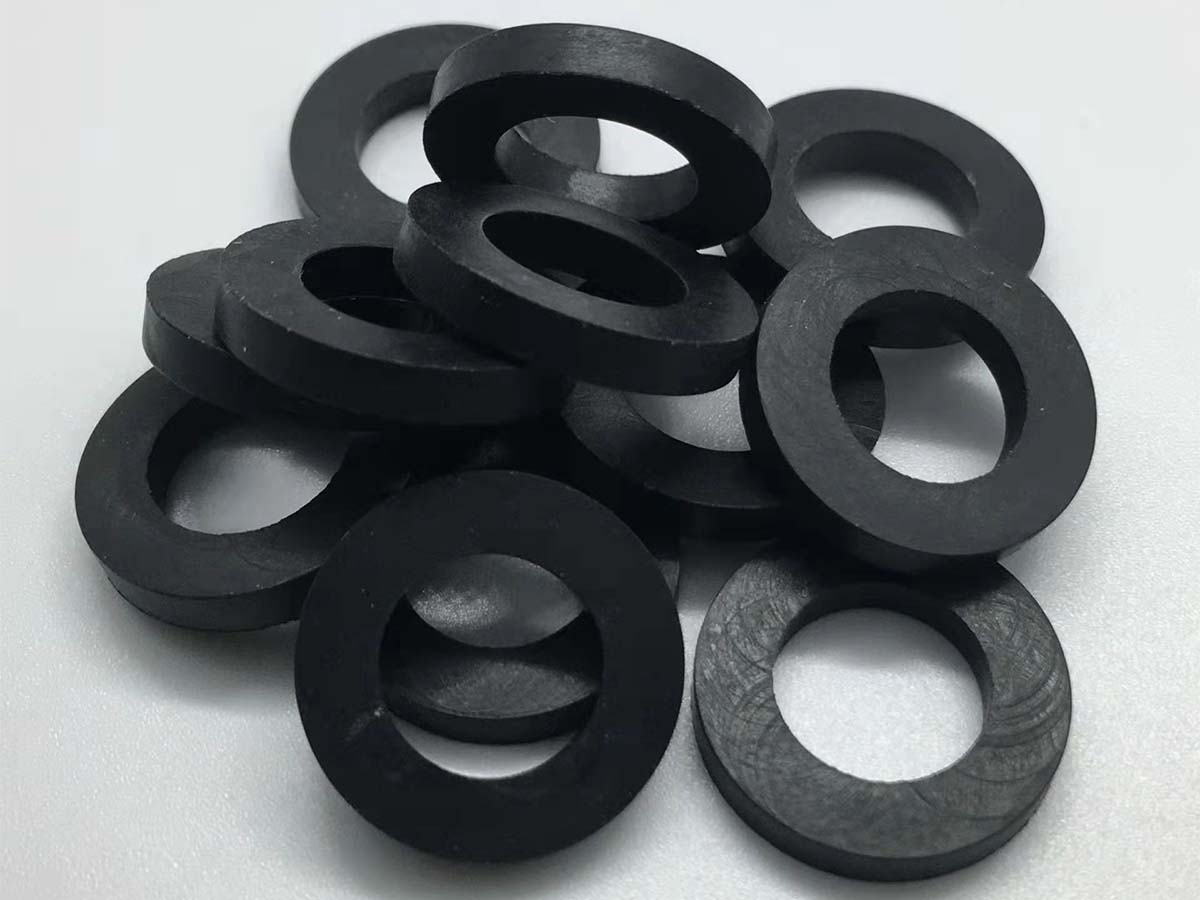
rubber
Technical Advantages
The unique curves on the roller and plate make grinding more efficient, creating a better material bed for higher output of quality products.
A compacting tool maintains fine grinding, while minimal mill vibration cuts energy waste. Quicker processing reduces over-grinding, lowering iron content for purer, whiter results.
A touch of additive boosts value without quality loss.
The CLUM mill uses multi-rotor classifiers to tailor powder fineness, avoiding waste. Its PLC system finely tunes grinding for consistent quality. With ultrafine grinding tech, it saves up to 50% energy, making it a cost-effective choice.
The mill features an advanced separator for a wide particle size range, with up to 70% 2μm powder, D97 from 4-45μm, and a surface area of 21000cm2/g.
It outputs primary powder at D97=8.5μm, and a secondary system captures 4-5μm particles, ensuring a high-value, well-shaped powder.
The mill’s grinding pressure is precisely managed by a PLC/DCS system for efficient, stable operation. Remote control is a breeze with the automatic system, and variable speed lets it handle tough materials.
Protection measures prevent roller damage, ensuring stable runs. The rollers have their own smart lube system to keep them cool and leak-free.
The grinding roller does not contact the grinding plate directly. Both the grinding roller and the lining plate are made of high-quality materials. Therefore, these parts enjoy long service life and high wear resistance.
The grinding roller can be turned out of the mill shell. This feature facilitates the inspection of the grinding roller and the replacement of the roller sleeve and lining plate, thus reducing downtime and labor costs.
The special structural design and operating principle of the mill ensure small vibration and low noise.
The whole equipment is well sealed and the system operates under negative pressure. Therefore, powder and dust are prevented from flowing out of the system. It is environmentally friendly and meets the national environmental protection requirements.
Main Structure
CLUM ultra-fine vertical mill main machine is mainly composed of motor, reducer, machine body, grinding roller device, grinding disc device, pressurizing device, powder separator, lubrication station, hydraulic station, etc.

Lubrication and Monitoring System
The reduction gearbox has lubricating oil flow, temperature, pressure detection, bearing temperature detection, vibration detection, and interlocking control with the DCS system.
High-Quality Reduction Motor
The reduction motor adopts German SEW or NORD brand, which has low power consumption, low failure rate and long service life.
Advanced Control System
The control system adopts Siemens PLC or DCS control system, which is reliable and advanced.
● The grinding roller and grinding disc are made of imported high wear-resistant materials, with long service life and low maintenance cost.
● The grinding area between the grinding roller and the grinding disc adopts a special grinding curve design to ensure stable operation of the main machine and effective grinding.
● The grinding roller pressurization adopts a hydraulic pull rod with adjustable elastic coefficient to ensure the continuous grinding force of the grinding roller on the material.
● There is no contact between the grinding roller and the grinding disc. Mechanical limit devices are used to avoid damaging impact vibrations.
● The multi-rotor high-efficiency cage powder separator has high powder selection efficiency and is easy to adjust and control. It can quickly produce finished products of various specifications.
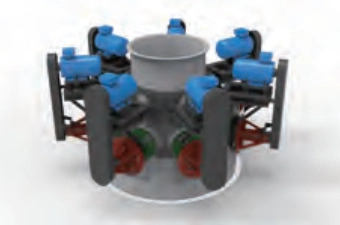
High-efficient multi-rotor concentrator
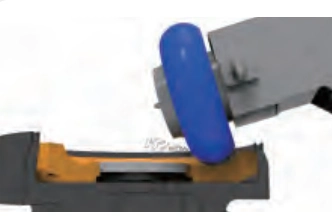
Special ultra-fine grinding device
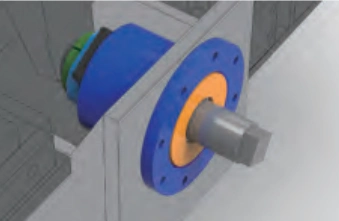
Safety mechanical limit device
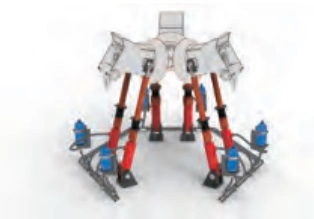
Precisely controlled pressurizing device
Composition of CLUM vertical roller mill production line
The CLUM ultra-fine vertical mill production line includes a primary powder making system (mainly raw material crushing, raw material transportation, ultra-fine grinding and classification, finished product collection, finished product transportation, finished product storage, and auxiliary equipment) and a secondary powder selection system (mainly It consists of multi-rotor ultra-fine powder separator, fan, pulse dust collector, elevator, discharge valve, screw conveyor and finished product tank).
Working Principle
The material shaken passes through the screw feeder and falls into the center of the grinding plate. The host drives the reducer to drive the centrifugal force generated by the rotation of the grinding plate, causing the material to move evenly around the grinding plate. When the material passes through the roller path area on the grinding disc, it is crushed by the grinding roller, and the large pieces of material are directly crushed, and the smaller particles are squeezed to form a material bed for inter-particle crushing.
After being crushed, the materials continue to move toward the edge of the grinding plate, and are taken to the powder separator for classification by the airflow entering from the air inlet. Under the action of the blades of the powder separator, the powder that does not meet the particle size requirements falls into the grinding disc and is ground again. The powder that reaches the standard passes through the powder separator and enters the pulse dust collector with the air flow for collection. The collected and discharged powder is the finished powder.
Impurities such as iron blocks mixed in the material are difficult to grind and have high gravity. When passing through the edge of the grinding disc, they cannot be carried away by the airflow and fall into the lower chamber of the mill. They are sent to the slag spit by the scraper and discharged from the outside of the main machine.
Operation process of CLUM vertical roller mill production line
The CLUM series ultra-fine vertical mill production line is a new type of ultra-fine grinding equipment that integrates grinding, grading, transportation, secondary powder selection, and finished product packaging. The product fineness can reach 400-3000 mesh. The production line adopts advanced technology, has high production efficiency and finished product quality, has a high degree of automation, is simple to operate and easy to maintain.
Powder Production Process Flow
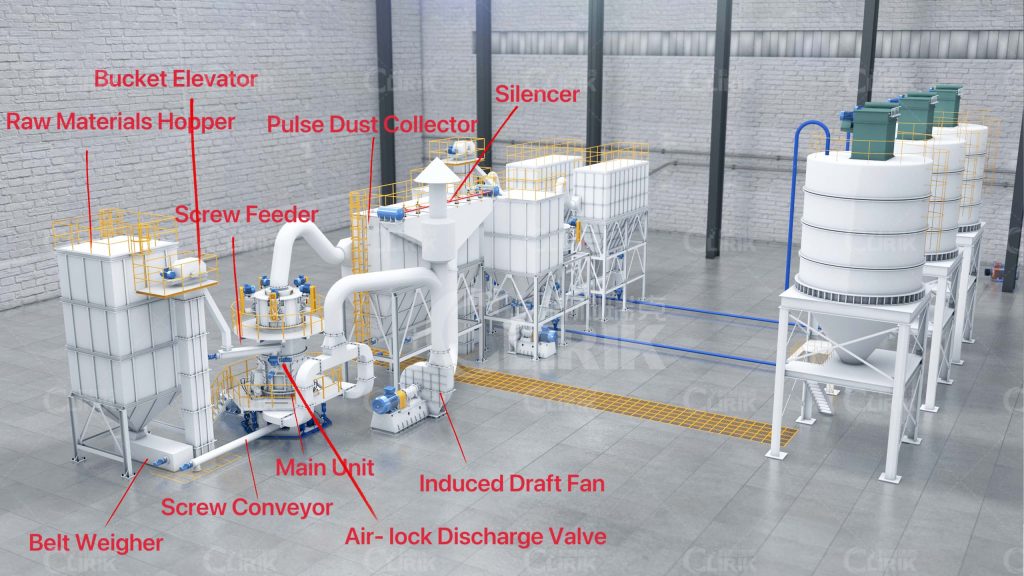
Secondary Classifying System
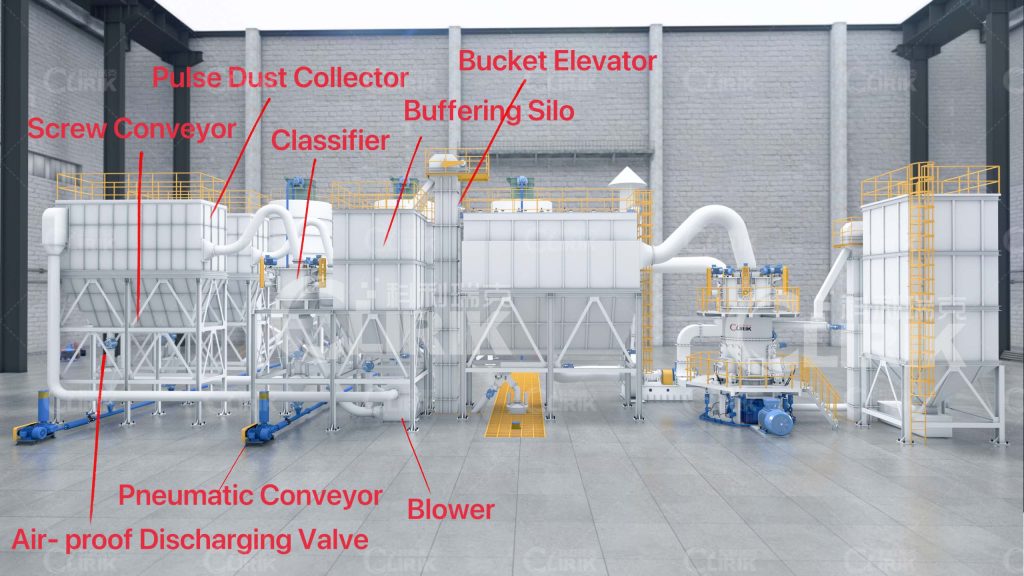
Parameters
Model | CLUM1425 | CLUM1632 | CLUM1736 |
Working Diameters (mm) | 1400 | 1600 | 1700 |
Number of rollers (pieces) | 3 | 3 | 3 |
Number of classifier (pieces) | 6 | 6 | 6 |
Power of classifier (Kw) | 6×15 | 6×22 | 8×22 |
Main unit power (Kw) | 250 | 315 | 380 |
Blower power (Kw) | 200 | 250 | 315 |
Feed size (mm) | <10mm | <10mm | <10mm |
Moisture of feeding material | <3% | <3% | <3% |
Less than 2μm=34% output (t/h) | 9.5-11.5 | 12-14 | 14-16 |
Less than 2μm=50% output (t/h) | 4.5-5.5 | 5.6-7 | 6.7-8.4 |
Less than 2μm=70% output (t/h) | 1.5-2.5 | 1.9-3.2 | 2.3-3.8 |
Particle size distribution: measured by micro laser diffraction particle size analyzer in British Malvern 3000 instruments
Comparison between CLUM vertical mill and ball mill
Vertical mills and ball mills are both commonly used industrial grinding equipment, but they have certain differences in working principles, applicable materials, finished product fineness, production capacity, energy consumption, etc. So how do we choose the most suitable grinding equipment? The following is a simple comparison between vertical mills and ball mills to help you choose a more suitable grinding equipment.
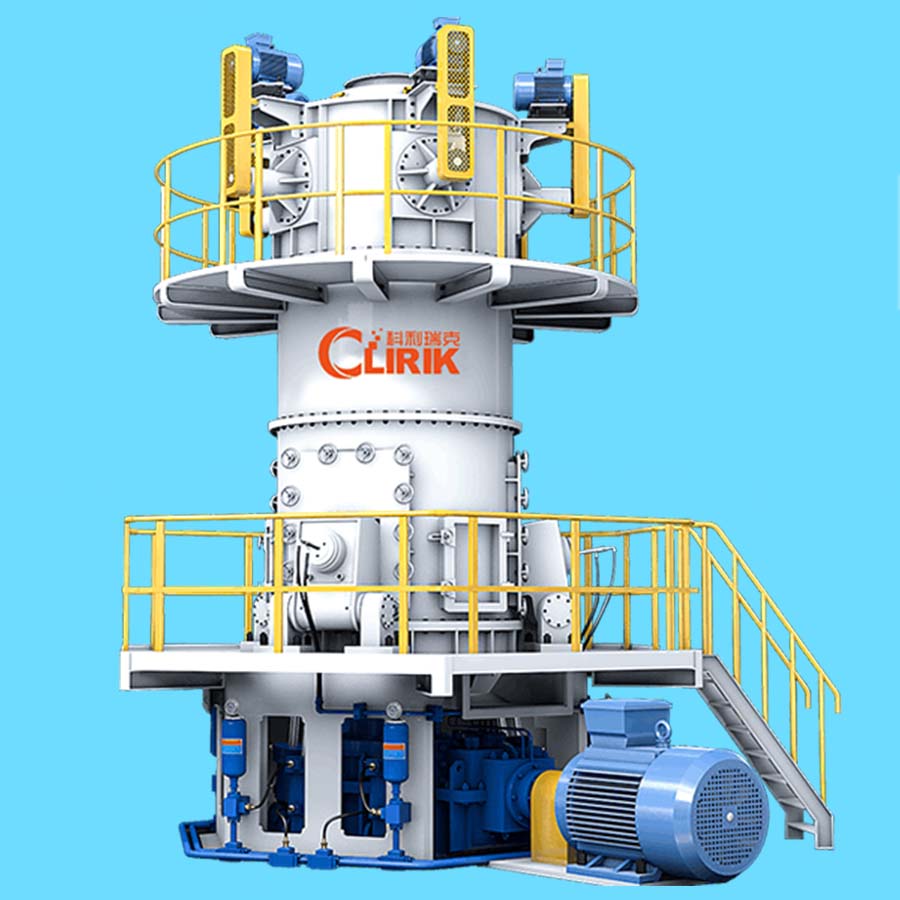
The vertical grinding mill adopts the principle of “material bed grinding“. The material forms a material bed on the grinding disc. Through the action of roller pressure and centrifugal force, the material particles rub and collide with each other to be crushed
Main structural components: grinding disc, grinding roller, separator, dust collector
The discharge fineness of the vertical roller mill can reach 3000 mesh. Suitable for materials with medium hardness, brittleness and non-stickiness
- High grinding efficiency and low energy consumption; 2. Uniform product fineness and less over-crushing; 3. Less pollution and low operating costs
The finished powder has high whiteness and slightly worse sphericity than the ball mill
Efficient and flexible control of product categories, enabling conversion of different raw materials on one machine in a short time
VS
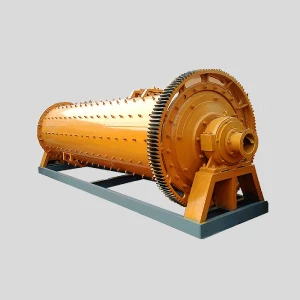
The ball mill adopts the principle of “media grinding“. The grinding chamber is filled with a certain number of steel balls or steel rods, and the materials are crushed under the impact and grinding action of the steel balls or steel rods
Main structural components: cylinder, lining plate, grinding ball, transmission device
The discharge fineness of the ball mill is generally between 20 and 200 mesh. Suitable for materials of various hardnesses, wider scope of application
- Wide application range and strong adaptability; 2. Good grinding effect and adjustable product fineness; 3. Simple structure and easy maintenance
The finished product has lower whiteness and better sphericity
Converting different raw materials on the same mill to produce different products requires a longer cleaning time
Comparison between CLUM vertical mill and HGM ultrafine grinding mill
CLUM vertical mill and HGM ultra-fine mill are industrial ultra-fine grinding equipment independently developed and produced by CLIRIK. There are certain differences between these two types of equipment in terms of working principles, production capacity, and finished product fineness. We can choose the most suitable grinding mill according to different production needs.
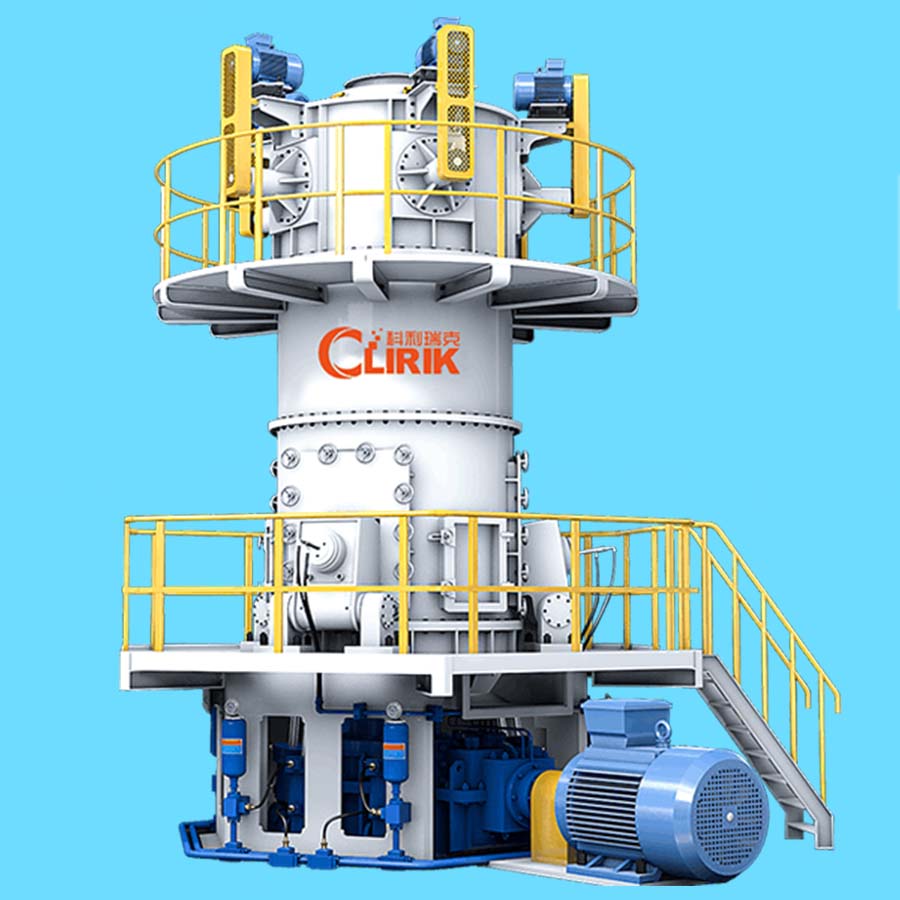
Low energy consumption, the electricity cost is 20%-30% lower than that of HGM mill under the same conditions
The ultra-fine vertical mill has a high content of 2 μm and a small average particle size D50; the price of the finished product is higher than that of the HGM mill
There is little iron contamination during the grinding process, and the finished powder has high whiteness and good sphericity
High grinding efficiency, low wear and long service life of wearing parts
There is a material return device, the production environment is clean, and the host machine has low noise
High initial investment cost and large floor area
VS
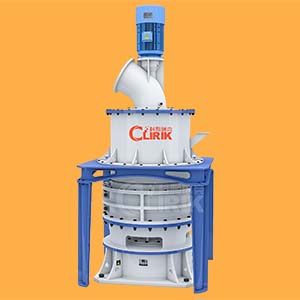
Compared with CLUM ultra-fine vertical mill, energy consumption is 20%-30% higher
The 2μm content is lower than that of CLUM vertical mill, and the average particle size D50 is larger; the finished product price is lower than that of CLUM mill
Iron contamination during the grinding process is relatively high, the finished powder has low whiteness and slightly poor sphericity
The grinding efficiency is lower than that of the CLUM mill. Normally, wearing parts need to be replaced once a year
There is no return device, and the cleanliness of the production environment is slightly poor. The host machine is noisy, and a soundproof room is usually required
Small initial investment cost and small floor space