Products
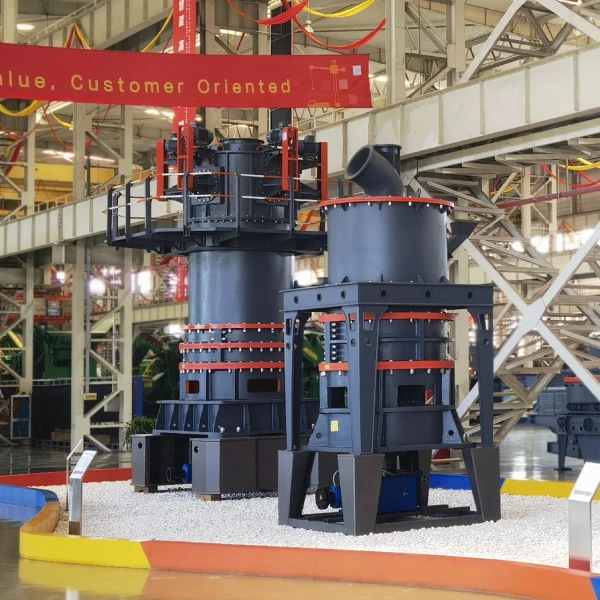
GRINDING MILLS
Non-metallic ore powder grinding
CLIRIK’s grinding equipment includes Raymond mill, ring roller mill, vertical roller mill, etc., which can produce 50-3000 mesh non-metallic ore powder. It has the characteristics of stable operation, simple operation, convenient maintenance, long service life and high quality of finished products.
STONE CRUSHERS
Solid stone, construction waste crushing
CLIRIK’s crushing equipment includes jaw crushers, impact crushers, impact crushers, etc. It can be used alone or in combination to produce sand and gravel; it can also be used in the crushing link of the grinding production line. It has the characteristics of high productivity, simple operation and wide application range.
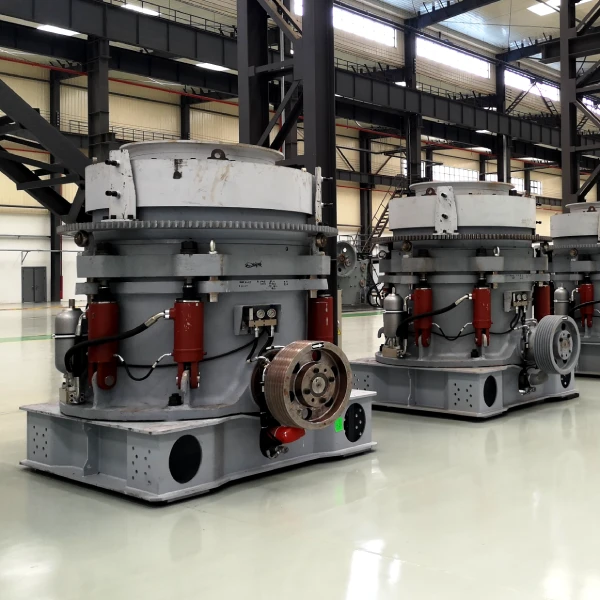
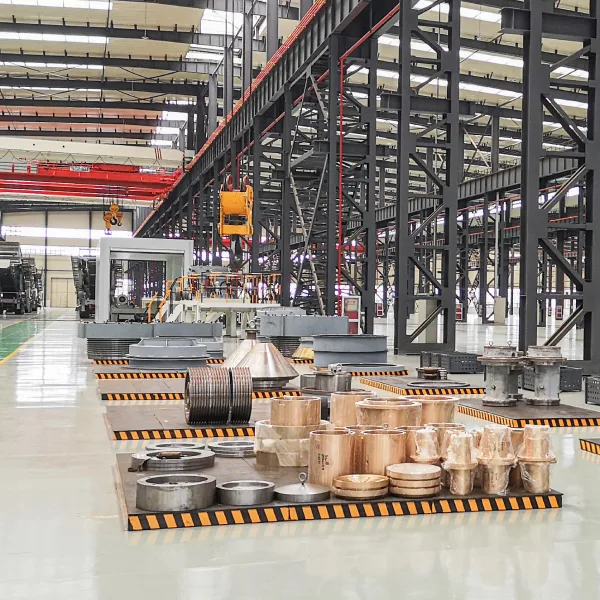
AUXILIARY EQUIPMENT
Auxiliary equipment is indispensable for a complete crushing and grinding production line, including conveyor belts, elevators, powder separators, powder collectors, packaging machines, dust collectors, etc. They connect various production links in series to make the production line smoother, more efficient, and more complete in performance.
Get Production Line Configuration Plan For Free!
Frequently asked Questions
What should you pay attention to when purchasing an ore grinding machine?
- Understand the type of ore: The hardness, density and moisture content of the ore will affect the choice of grinding mill.
- Clarify the output and fineness requirements, and select a grinding mill that can meet the requirements.
- Understand the performance, energy consumption, environmental protection, finished product quality, etc. of the grinding mill, and choose the best one within your budget.
- Choose a regular manufacturer, and if possible, conduct on-site inspections and test machines to ensure that the grinding mill can meet the needs.
How to maintain ore grinding mill?
The maintenance of ore grinding mill can be divided into daily maintenance, regular maintenance and abnormal maintenance.
Routine maintenance
Routine maintenance is the basis for ore grinding mill maintenance, which mainly includes the following:
Regular maintenance
Regular maintenance is an important part of the maintenance of ore grinding mill, which mainly includes the following:
Abnormal maintenance
Abnormal maintenance refers to maintenance work performed when equipment fails. The main contents include:
Overhaul
Maintenance is the highest level of maintenance for ore grinding mills, which mainly includes the following:
Precautions for maintenance of ore grinding mill:
During maintenance, you should strictly follow the instructions of the equipment to avoid causing damage to the equipment.
Use special tools for maintenance to avoid damaging equipment parts.
When cleaning the inside of the equipment, care should be taken to avoid inhaling dust.
When replacing severely worn parts, parts with the same specifications as the original parts should be selected.
By doing a good job in the maintenance of the ore grinding mill, the service life of the equipment can be extended, the operating efficiency of the equipment can be improved, and the production cost can be reduced.
What are the maintenance measures for ore grinding mill?
Specific maintenance measures are as follows:
- Check the connection of each component of the equipment
Before normal operation of the equipment, check the connection status of each component of the equipment to ensure that the connections are tight and reliable. If any loose or falling parts are found, they should be tightened or replaced in time. - Check the operating status of the equipment
During the normal operation of the equipment, attention should be paid to checking the operating status of the equipment and handling any abnormalities in a timely manner. If abnormal vibration, excessive noise, excessive temperature, etc. are found in the equipment, it should be stopped immediately for inspection. - Clean the outside of the device
During normal operation of the equipment, the outside of the equipment should be cleaned regularly to prevent dust and debris from accumulating. The accumulation of dust and debris will affect the heat dissipation of the device, causing it to overheat or even be damaged. - Check the lubrication of the equipment
During the normal operation of the equipment, the lubrication condition of the equipment should be checked regularly and the lubricating oil should be replenished in time. Insufficient lubrication can lead to increased equipment wear and even damage. - Replace wearing parts such as grinding rollers and grinding rings
The grinding roller and grinding ring are wearing parts of the ore grinding mill and should be replaced regularly. Severe wear of the grinding roller and grinding ring will affect the grinding effect of the equipment and even cause damage to the equipment. - Clean the inside of the device
After the equipment has been running normally for a period of time, the inside of the equipment should be cleaned to prevent material accumulation. Material accumulation will affect the grinding effect of the equipment and even cause damage to the equipment. - Check the equipment’s electrical system
During the normal operation of the equipment, the electrical system of the equipment should be checked regularly to ensure safety and reliability. Faults in the electrical system can cause equipment shutdowns and even cause safety accidents. - Check the bearings, gears and other parts of the equipment
After the equipment has been running normally for a period of time, the bearings, gears and other components of the equipment should be checked to ensure normal operation. Serious wear of bearings, gears and other components will affect the operating efficiency of the equipment and even cause damage to the equipment. - Find the cause of the fault and eliminate it in time
When equipment fails, the cause of the failure should be found promptly and measures should be taken to eliminate the failure. If you are unable to troubleshoot the problem yourself, you should promptly ask a professional to perform repairs. - Replace damaged parts
When equipment fails, damaged parts should be replaced promptly. If damaged parts are not replaced in time, other parts of the equipment will be damaged or even the equipment will be scrapped.
What equipment does a complete ore grinding production line include?
A complete ore grinding production line usually contains the following equipment:
Crusher: Used to break raw ore into small pieces for grinding by the mill. Commonly used crushers include jaw crushers, impact crushers, cone crushers, etc.
Pulverizer: used to crush the crushed ore into the required fineness. Commonly used grinding mills include Raymond mill, ultrafine grinding mill, vertical roller mill, etc.
Feeder: used to feed the crushed ore evenly into the grinding mill. Commonly used feeders include vibrating feeders, screw feeders, etc.
Powder separator: used to sort the powder from the mill according to particle size. Commonly used powder separators include gravity powder separator, air flow powder separator, etc.
Dust collector: used to collect dust generated during the grinding process. Commonly used dust collectors include bag dust collectors, cyclone dust collectors, etc.
Conveyor: used to transport the ground powder to the next process or storage. Commonly used conveyors include belt conveyors, screw conveyors, etc.
Powder collector: used to store finished powder.
Packaging machine: used to pack finished powder.
Silencer: A silencer can be configured according to needs to reduce noise and make the production environment more friendly.
Can CLIRIK customize production line solutions for customers?
CLIRIK provides customers with services for configuring production lines.
First, we will understand your specific needs, including:
Type, output, particle size, hardness, etc. of raw materials
Product type, output, particle size, quality, etc.
Equipment budget
Production line site conditions, etc.
Secondly, analyze the process flow
Determine the process flow of the production line based on the type, output, particle size, hardness, etc. of raw materials, as well as the type, output, particle size, quality, etc. of the product.
Then, select the device
Select appropriate equipment according to the requirements of the process flow. We will consider the following factors:
Equipment performance parameters, such as crushing ratio, output, energy consumption, etc.
Equipment wear resistance
price of equipment
Then, perform an economic analysis
Based on the selection of equipment, conduct an economic analysis to determine the investment cost and operating cost of the production line.
Finally, provide a program report
The plan report includes: production line overview, process flow, equipment configuration, and economic analysis.