Jaw Crusher
Jaw crushers are suitable for crushing ores that are hard and soft, with a compressive strength of less than 320 MPa. This machine can reduce materials to medium and fine sizes.
Input size:
<850mm
Capacity:
1-500t/h
Power:
5.5-110kw
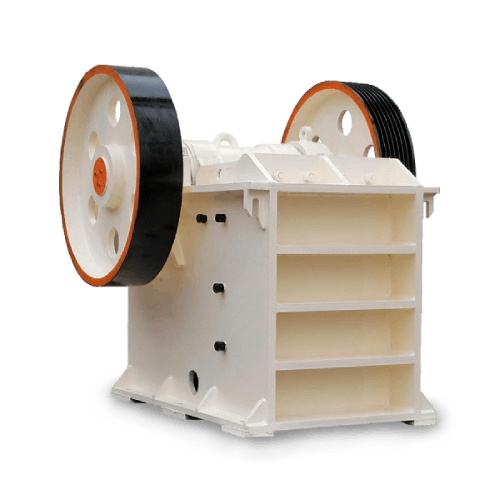
Scope and Application
This is a category of crushers that are extensively utilized in both the initial and subsequent stages of the crushing process.
It is mainly used in the industries of metallurgy, mining, chemical, cement, construction, refractory materials and ceramics.
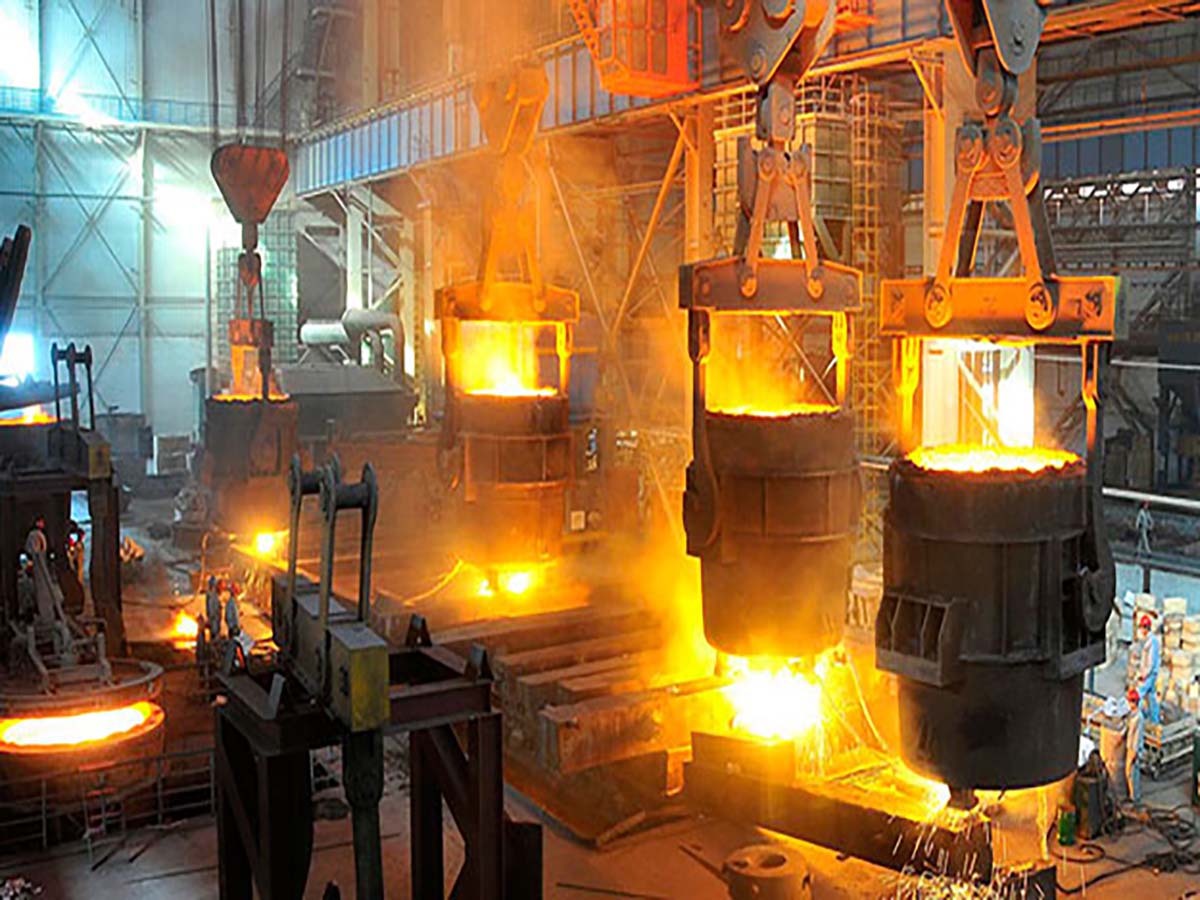
metallurgy
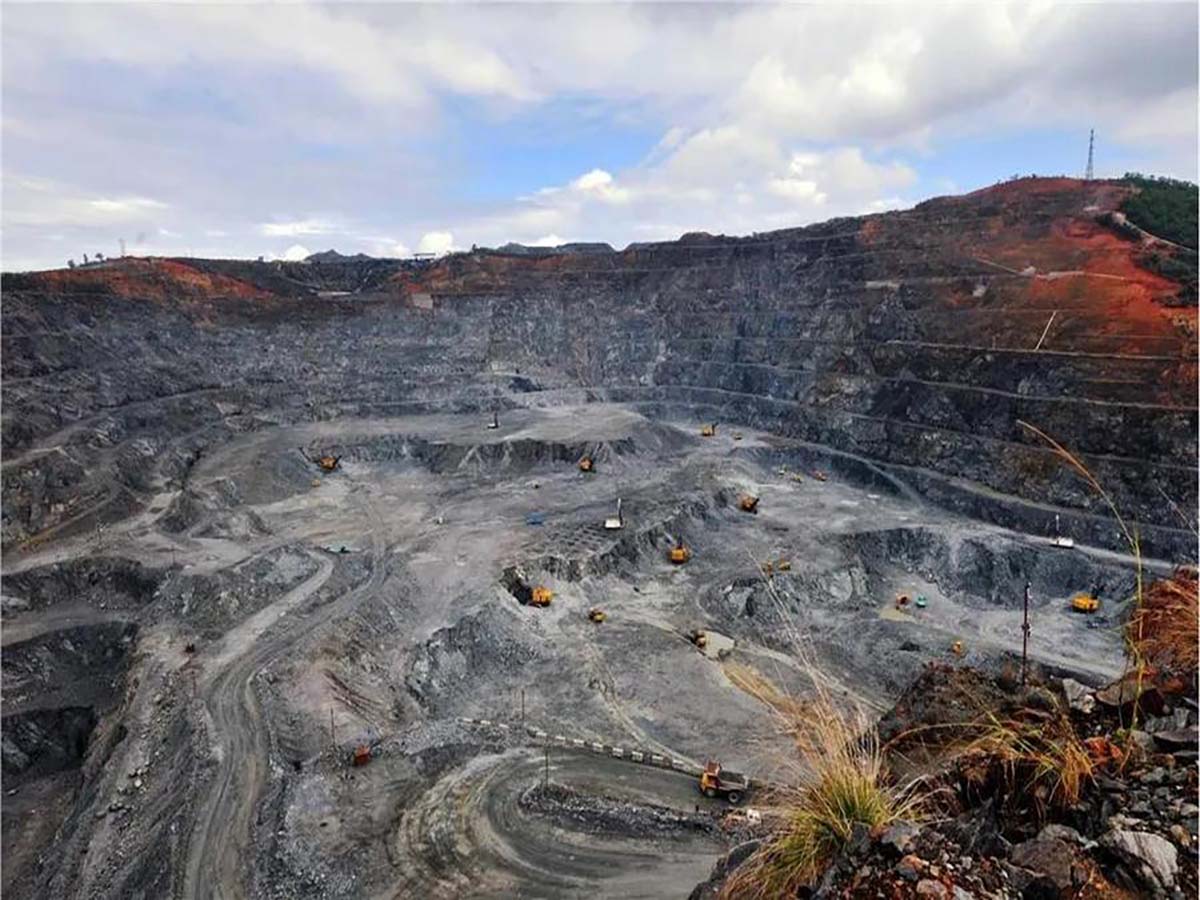
mining
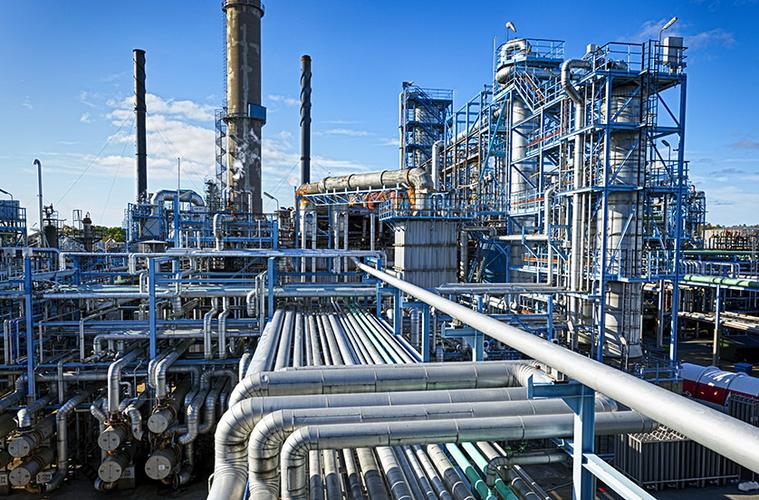
chemical
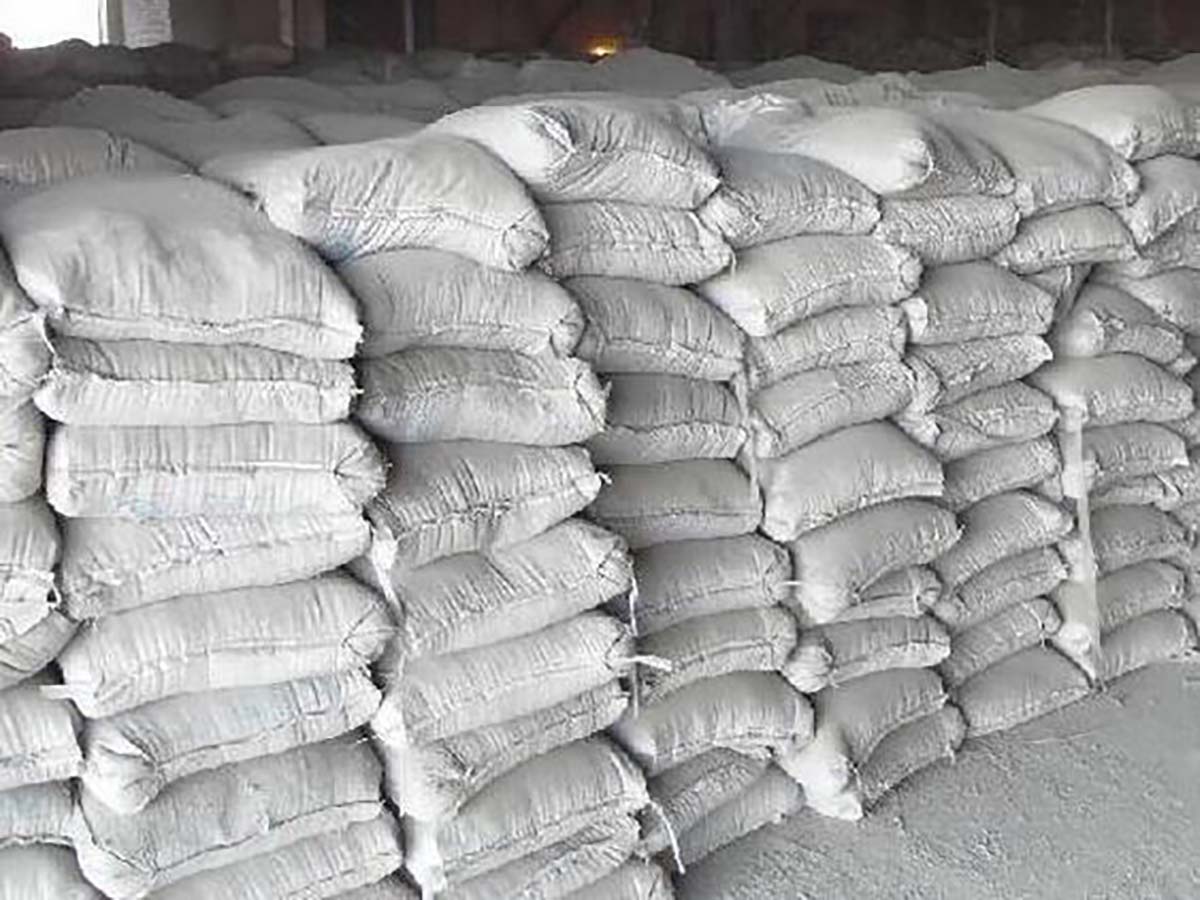
cement
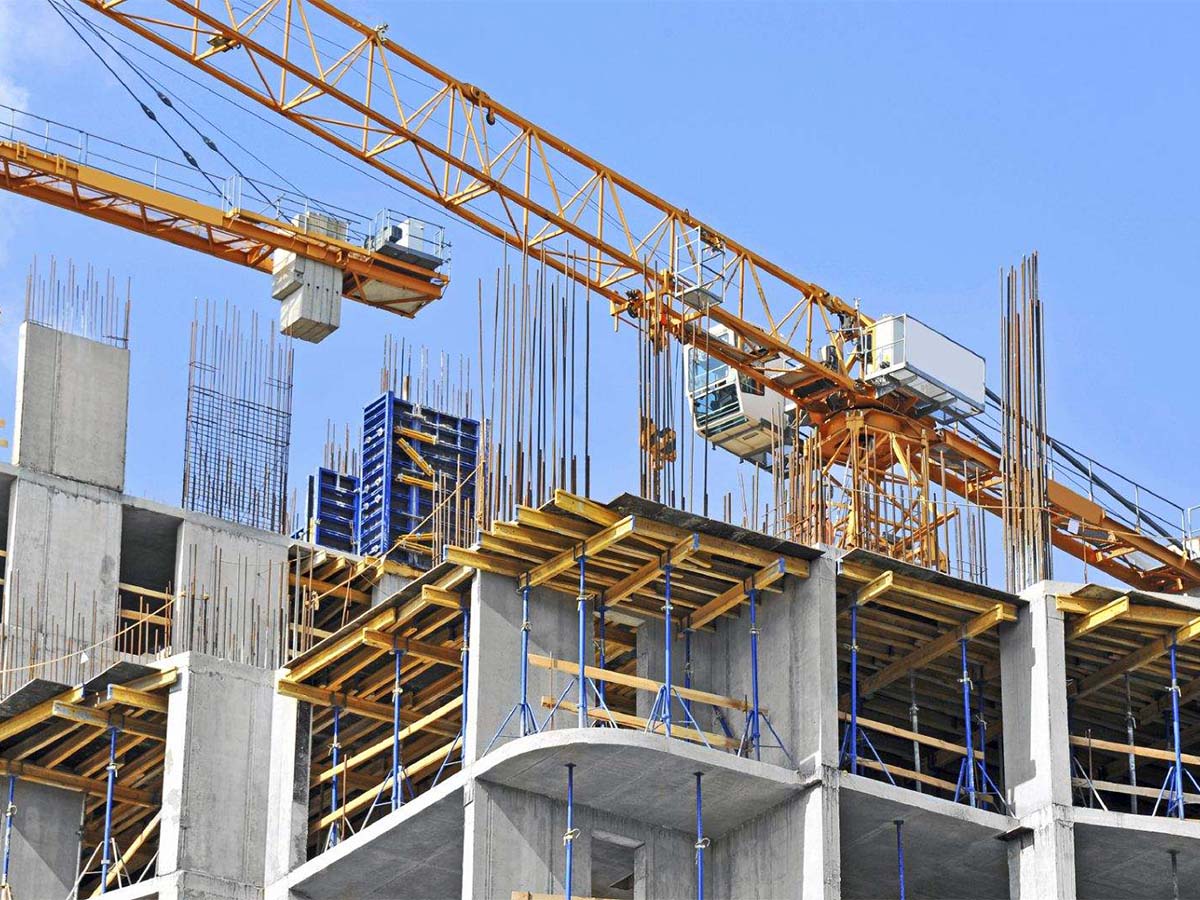
construction
Technical Advantages
The jaw crusher excels at efficiently crushing large amounts of material into smaller sizes. Its design ensures high performance and precision, making it ideal for industries that demand uniform, high-quality output.
The jaw crusher’s simple structure is the foundation of its reliability. With fewer moving parts, it reduces the potential for mechanical issues, ensuring consistent operation.
The jaw crusher is user-friendly, designed for easy operation and maintenance. Its intuitive controls and accessible components reduce the need for specialized knowledge or tools.
Working Principle
The moving part of the crusher goes up and down, powered by a motor. It opens to let material in and closes to crush it.
During the upward movement of the movable jaw, materials are subjected to a force that crushes them against the stationary fixed jaw plate. The pressure exerted by the movable jaw plate ensures that the materials are effectively crushed to the desired size.
When the movable jaw descends, the angle between it and the bracket decreases, which allows the crushed materials to be released from the crushing cavity. The force of the spring and the connecting bars assists in this process, ensuring that the crushed materials of the correct size are discharged efficiently.
The motor’s continuous rotation maintains the cyclical motion of the movable jaw, which crushes and discharges materials in a repetitive process. This ongoing cycle is essential for achieving high-volume production goals.
Parameters
Model | Feeder Size (mm) | Input Size (mm) | Output Range (mm) | Capacity (t/h) | Power (kw) | Dimension (mm) |
PE 150*250 | 150*250 | 125 | 10—40 | 1—5 | 5.5—7.5 | 922*745*933 |
PE 200*300 | 200*300 | 125 | 15—30 | 2—10 | 7.5 | 935*750*990 |
PE 200*350 | 200*350 | 125 | 15—40 | 5—16 | 7.5—11 | 1056*1142*1220 |
PE 250*400 | 250*400 | 210 | 20—60 | 5—20 | 15—18.5 | 1430*1310*1340 |
PE 400*600 | 400*600 | 350 | 40—100 | 15—60 | 30—37 | 1700*1732*1653 |
PE 500*750 | 500*750 | 425 | 50—100 | 40—100 | 45—55 | 2035*1921*2000 |
PE 600*750 | 600*750 | 465 | 60—140 | 50—120 | 50—65 | 2150*1988*2105 |
PE 600*900 | 600*900 | 480 | 65—160 | 60—140 | 55—75 | 2290*2106*2370 |
PE 750*1060 | 750*1060 | 550 | 75—200 | 75—160 | 60—85 | 4180*2560*3070 |
PE 1000*1200 | 1000*1200 | 850 | 195—265 | 315—500 | 110 | 3480*2876*3330 |
PEX 150*750 | 150*750 | 120 | 18—48 | 8—25 | 7.5—75 | 1200*1530*1060 |
PEX 250*400 | 250*400 | 210 | ≤12 | 5—10 | 15—18.5 | 1430*1310*1340 |
PEX 250*1000 | 250*1000 | 210 | 25—60 | 16—50 | 30—37 | 1530*1992*1380 |
PEX 250*1200 | 250*1200 | 210 | 25—60 | 20—60 | 37—45 | 2192*1605*1415 |
PEX 300*1300 | 300*1300 | 250 | 25—105 | 20—90 | 75 | 2720*1950*1600 |