Impact Crusher
Impact Crusher can crush many kinds of materials with max feed size less than 500mm and crushing strength less than 360 MP.
Input size:
≤500mm
Discharging size:
400-3000mesh
Capacity:
10-350t/h
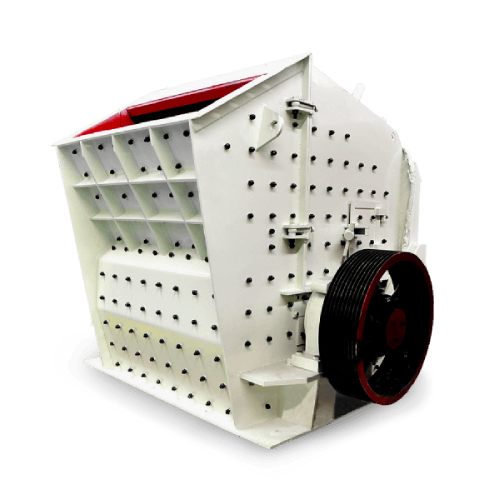
Scope and Application
Impact crusher is the latest generation of impact crusher developed by our company in absorbing advanced technology at home and abroad, combined with the specific working conditions of the domestic sand and gravel industry.
The most outstanding advantage of impact crusher is that its finished powder is in good, cubic shape, non-tensile and cranny.
It is widely used in mining, transportation, energy, construction and chemical industry.
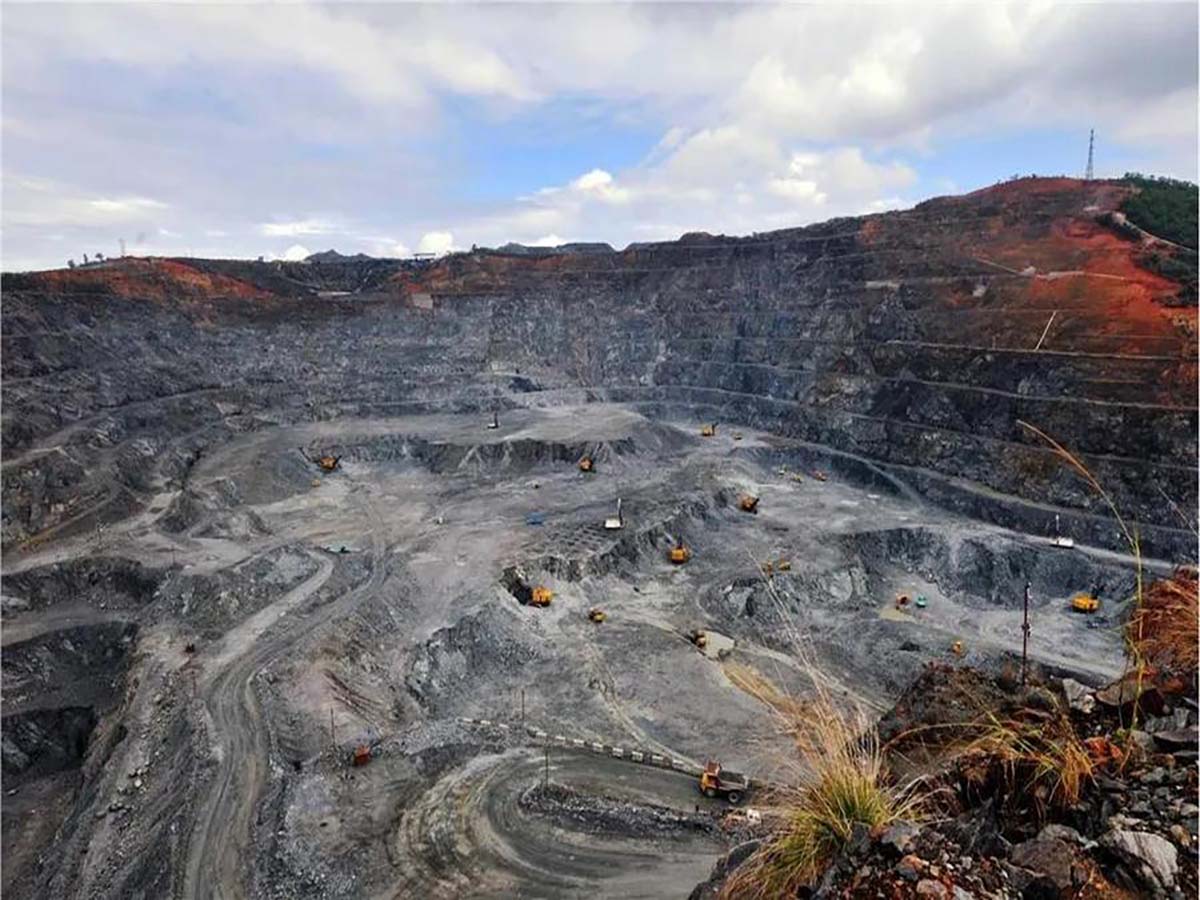
mining
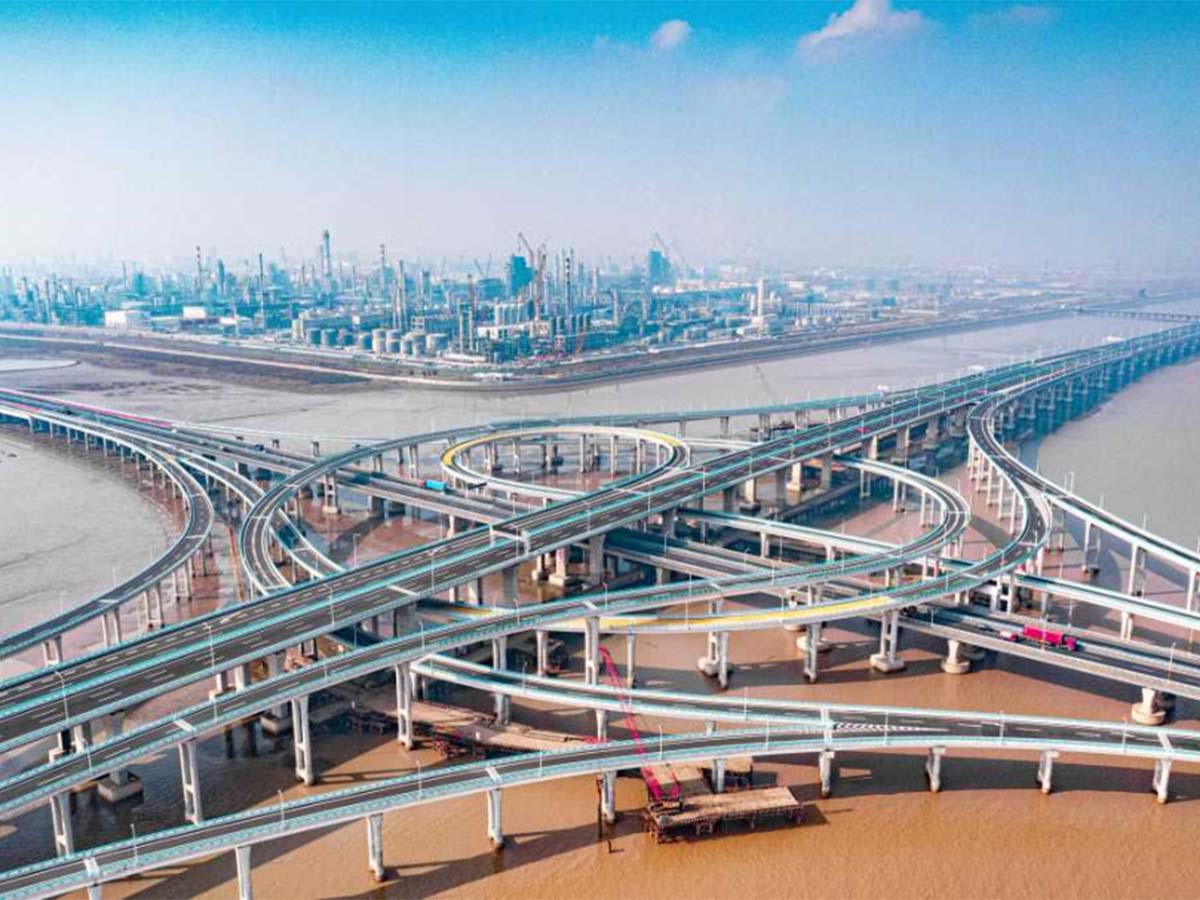
transportation
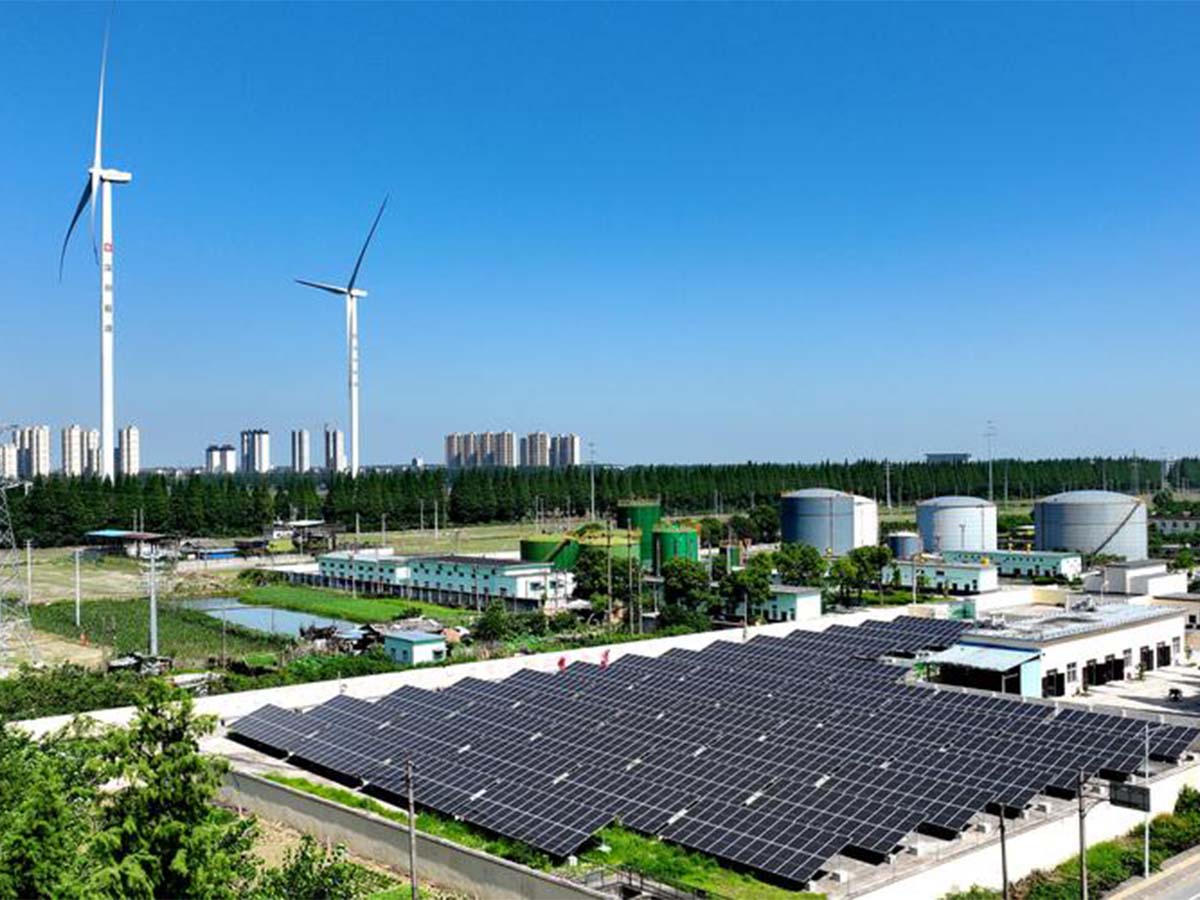
energy
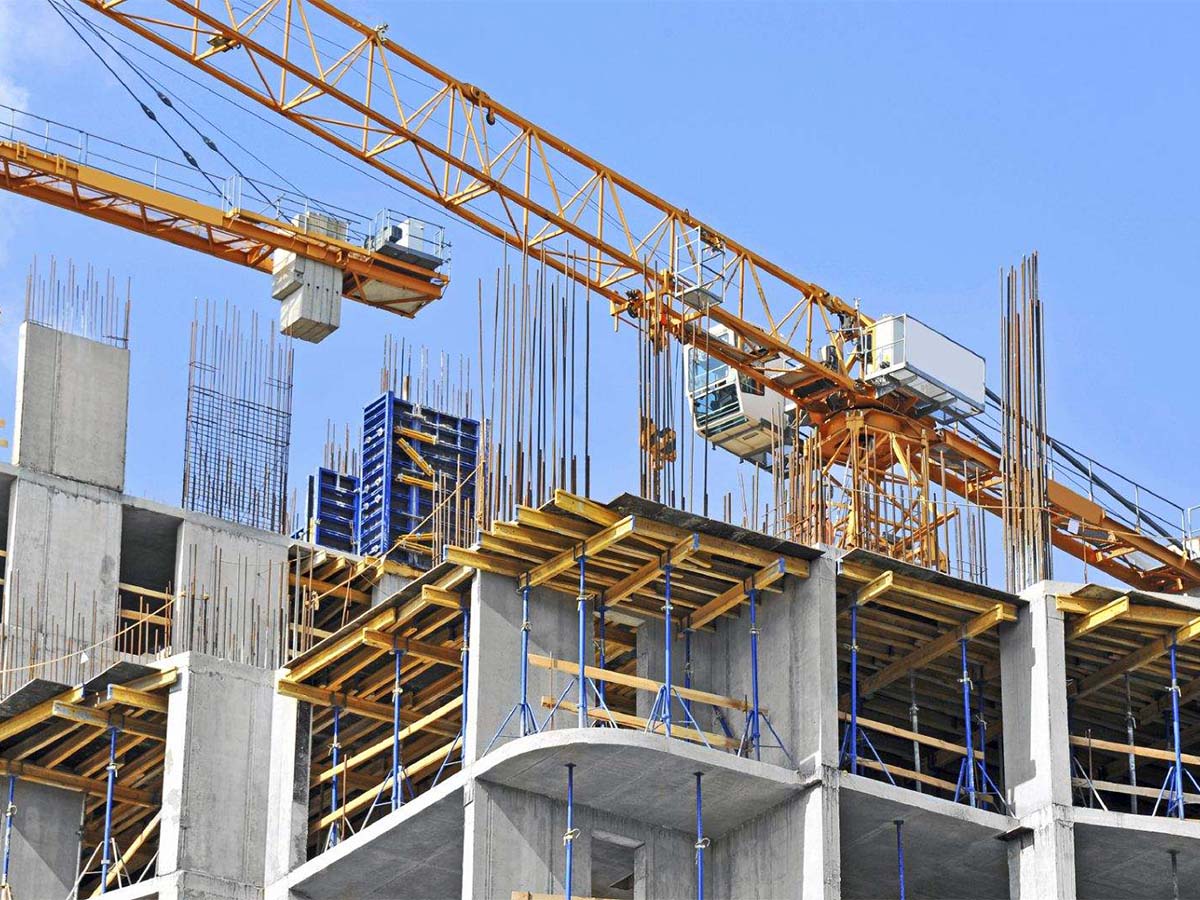
construction
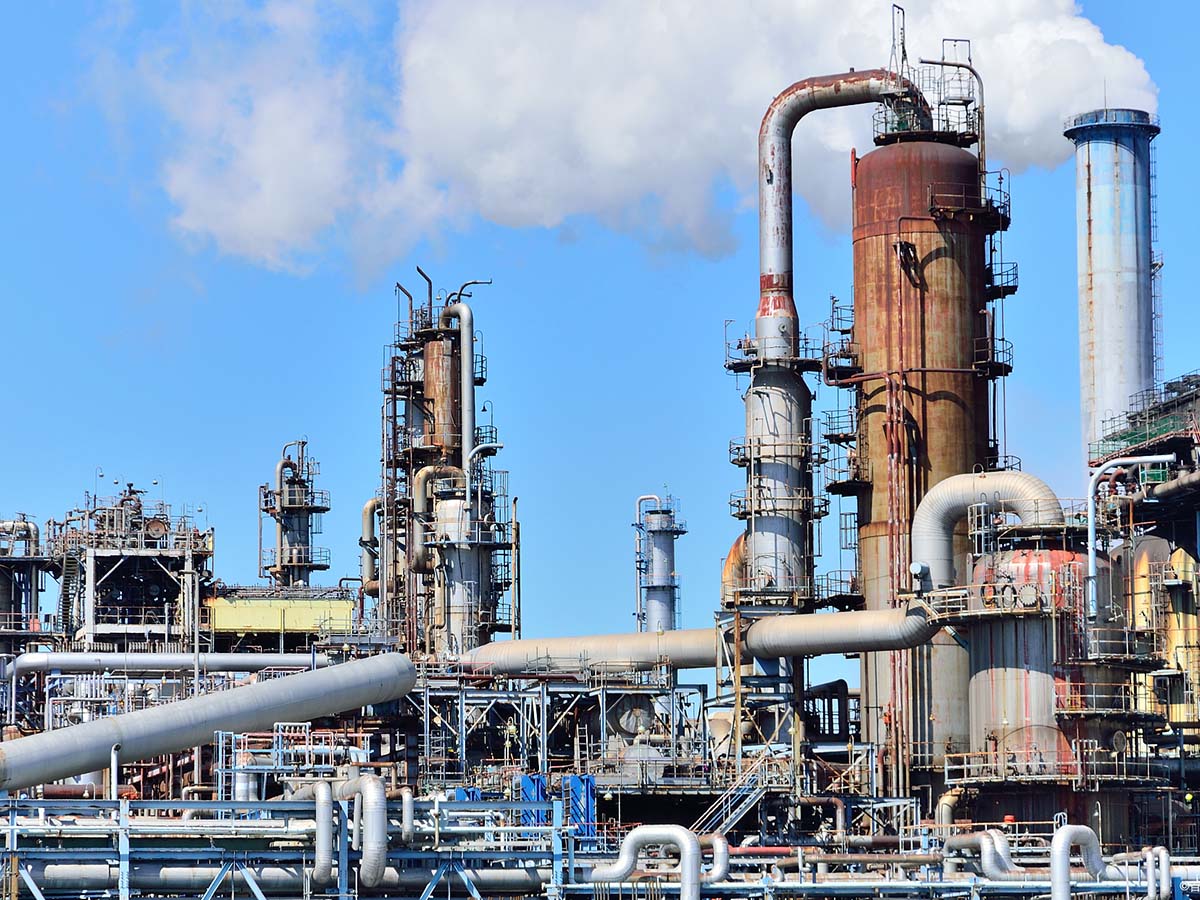
chemical
Technical Advantages
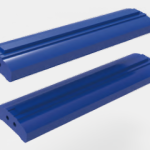
The impact crusher is equipped with hammers made from high chrome, a material known for its exceptional hardness and resistance to wear.
The liner board, constructed from wear-resistant materials, ensures longevity and minimizes the need for frequent replacements, contributing to the crusher’s overall durability and reliability.
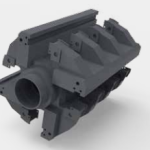
The impact crusher features a specially designed tooth impact plate that is highly efficient in crushing hard rock.
This innovative design enhances the crusher’s performance, resulting in high efficiency and low energy consumption, making it an ideal choice for challenging crushing tasks.
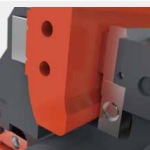
A key advantage of the impact crusher is its ability to produce a final product with a cubic shape.
This shape is highly desirable in various applications as it is non-tensile and free from cracks, ensuring a high-quality end product that meets stringent industry standards.
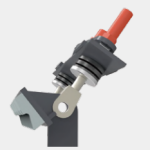
The impact crusher offers an adjustable discharge opening, allowing for customization of the particle size of the final product.
This feature provides flexibility in meeting the diverse requirements of different applications and ensures a consistent output quality.
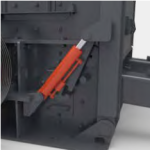
The design of the impact crusher simplifies the overall crushing process, making the flow chart more straightforward and efficient.
This simplification not only reduces the complexity of the system but also enhances the ease of operation and maintenance.
Detailed Structures
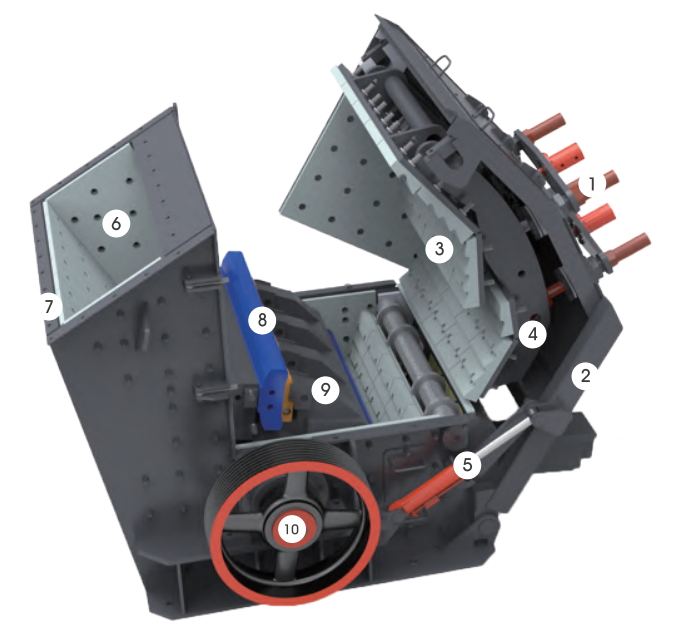
1. Hydraulic Regulation Device
2. Rear Frame
3. Impact Plate
4. Impact Rack
5. Hydraulic Jacking Device
6. Lining Plate
7. Front Frame
8. Hammer Bar
9. Rotor
10. Bearing House
Working Principle
The impact crusher functions by converting kinetic energy into impact energy for effective material crushing.
The process initiates as the motor powers the rotor to spin at a swift pace. This swift spinning is key to the crusher’s capability to produce the forceful impacts needed for crushing.
As the rotor spins, the blow bar, mounted on it, comes into play. When materials enter the operational zone of the blow bar, they are struck with force, causing them to disperse in the crushing chamber.
This initial impact is crucial for breaking down the material into smaller fragments.
Post the initial impact, the high-speed motion of the rotor causes the materials to rebound off the impact liner and return to the area influenced by the blow bar.
This rebound action subjects the materials to a continuous crushing process, ensuring they are progressively reduced in size until they meet the required specifications.
The final stage of the crushing process involves adjusting the clearance between the impact rack and the rotor.
This fine-tuning allows for the modification of the end product’s size and shape, catering to specific application needs and ensuring a consistent, high-quality output.
Specification
Model | Size (mm) | Feeder Size (mm) | Input Size (mm) | Capacity (t/h) | Motor (kw) | Weight (ton) |
PF-0608 | Φ644 x 740 | 320 x 770 | ≤ 100 | 10-20 | 30 | 4 |
PF-0807 | Φ850 x 700 | 400 x 730 | ≤ 300 | 15-30 | 30-45 | 8.13 |
PF-1007 | Φ1000 x 700 | 400 x 730 | ≤ 300 | 15-60 | 37-55 | 9.5 |
PF-1010 | Φ1000 x 1050 | 400 x 1080 | ≤ 350 | 50-90 | 55-75 | 14 |
PF-1013 | Φ1000 x 1300 | 650 x 1350 | ≤ 350 | 80-120 | 90-110 | 12 |
PF-1210 | Φ1250 x 1050 | 400 x 1080 | ≤ 350 | 70-130 | 110-132 | 17 |
PF-1214 | Φ1250 x 1400 | 400 x 1430 | ≤ 350 | 90-180 | 132-160 | 22 |
PF-1315 | Φ1320 x 1500 | 860 x 1520 | ≤ 400 | 120-250 | 180-260 | 26 |
PF-1320 | Φ1320×2000 | 860 x 2030 | ≤ 500 | 160-350 | 300-375 | 30 |