Industry Trends & Market Demand
As the world transitions to low-carbon energy, efficient coal utilization has become critical. Ultra-fine coal powder (400 mesh+) is gaining traction in coal chemical, power generation, and metallurgical industries due to its high combustion efficiency and low emissions. The Global Coal-Based Materials Market Report projects a 23% growth in demand by 2025, with Asia-Pacific accounting for over 60%. Shanghai Clirik’s CLRM-series Raymond Grinding Mill empowers industries to lead this transformation.
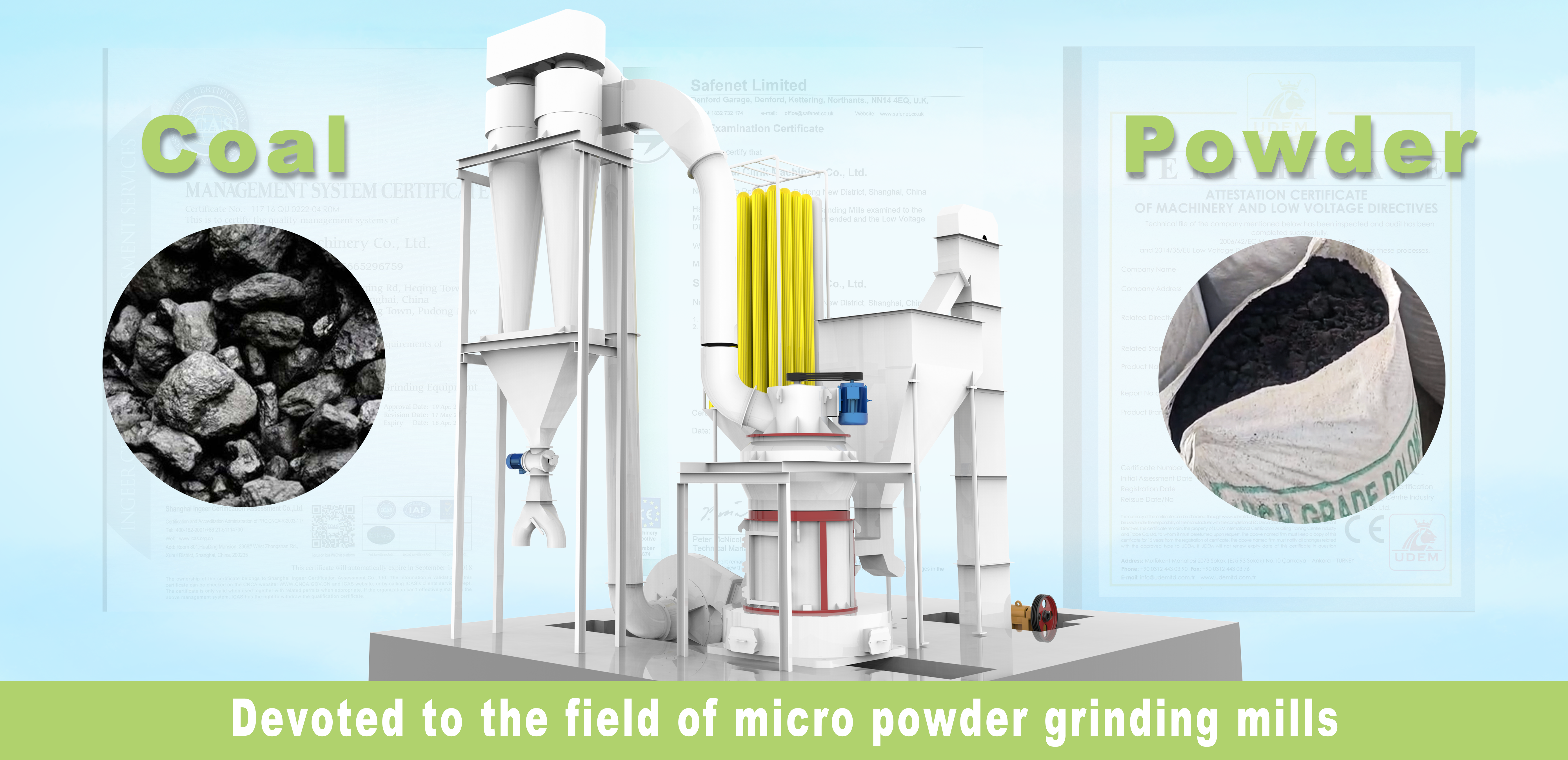
Technical Breakthroughs
- Core Innovations
- Dynamic Classifier System: Co-developed with German engineers, the turbine classifier offers stepless speed adjustment (85-145r/min), ensuring precise control from 80 to 500 mesh.
- Wear-Resistant Design: Combined with the hydraulic pressurizing device, the life span of the grinding rolls and rings is 3 times longer than that of traditional manganese steel parts, which reduces the frequency of downtime for replacement.
- Intelligent Safety: Infrared monitoring prevents spontaneous combustion by regulating grinding temperature, enhancing safety by 50%.
- Performance Comparison
Metric | Clirik CLRM-series Mill | Traditional Ball Mill |
---|---|---|
Fineness Range | Adjustable 80-500 mesh | Typically ≤200 mesh |
Energy Consumption | 18-25 kW·h/t | 35-50 kW·h/t |
Capacity (400 mesh) | 1-35 t/h | 0.5-5 t/h |
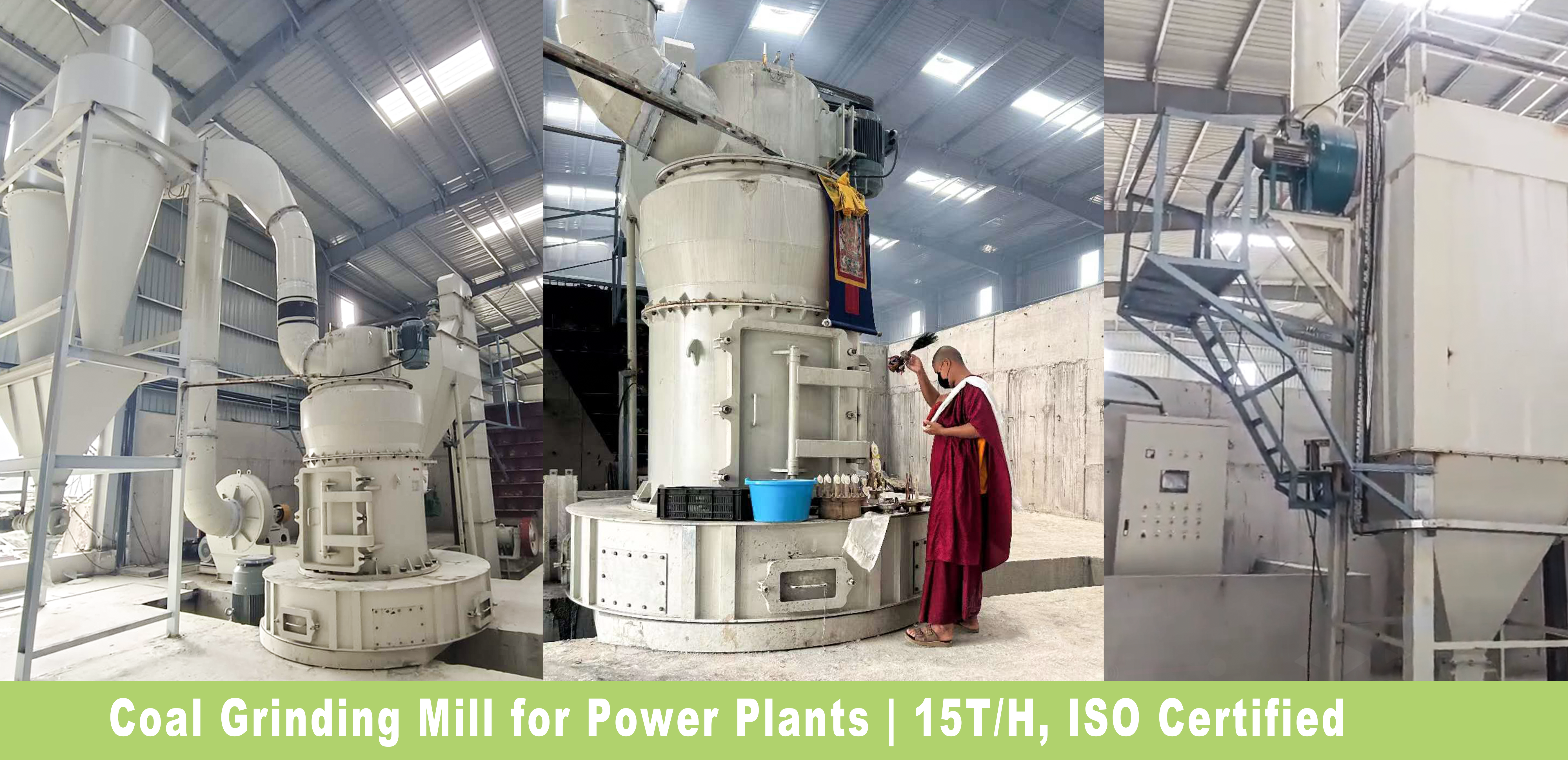
End-to-End Working Process
- Pre-Crushing: Raw coal is reduced to ≤20mm particles via jaw crusher.
- Grinding: Centrifugal force drives rollers to compress coal against the grinding ring.
- Classification: Airflow carries powder to a turbo classifier, where coarse particles (>400 mesh) are recycled, while fine powder is collected with 99.9% purity.
- Smart Control: PLC system auto-adjusts parameters for consistent D97 fineness (deviation <3%).
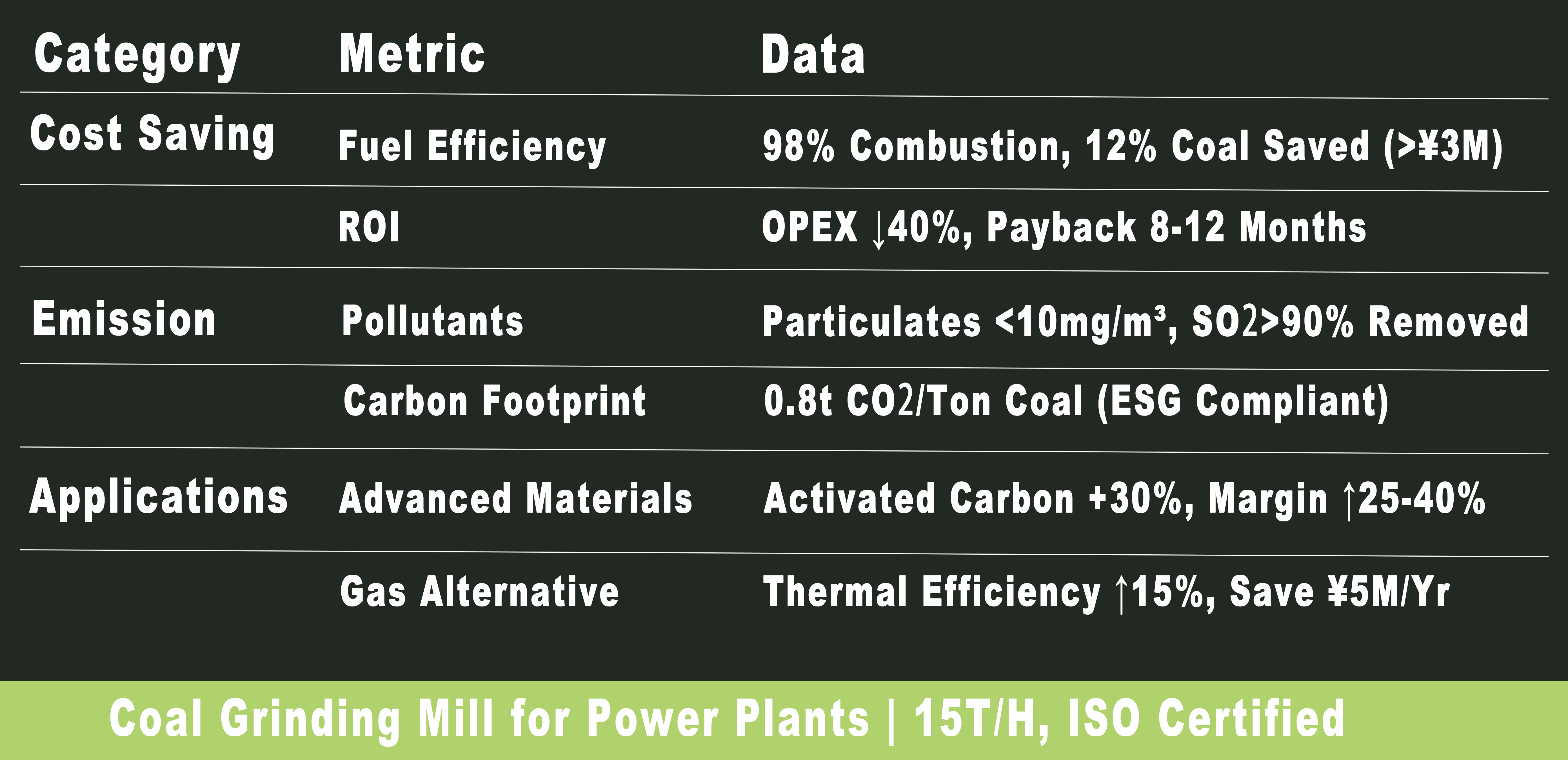
Why 400 Mesh Coal Matters?
- Economic Benefits
- Cost Savings: A Chinese power plant achieved 98% combustion efficiency, cutting coal consumption by 12% (annual savings: $450,000).
- ROI Optimization: With 2,000-hour maintenance intervals, Clirik mills reduce annual OPEX by 40%, achieving payback in 8-12 months.
- Environmental Compliance
- Emission Control: 400 mesh coal in CFB boilers reduces particulates to <10mg/m³ and SO₂ by 90%, exceeding EURO 6 standards.
- Carbon Reduction: Saves 0.8 tons of CO₂ per ton of coal burned, supporting ESG commitments.
- Industrial Applications
- Advanced Materials: Used in coal-derived activated carbon (+30% adsorption) and graphene precursors, boosting profit margins by 25-40%.
- Gas Alternative: Delivers 15% higher thermal efficiency than natural gas in ceramic kilns, offering a cost-effective transition solution.
Global Success Stories
- India: Two CLIRIK CLRM grinding mills upgraded lignite grinding for CFB boilers, achieving 94% combustion efficiency and 42,000-ton annual CO₂ reduction.
- Vietnam: Integrated dust removal systems ensured workshop dust <5mg/m³, securing ISO 14001 certification.
Why Choose Clirik?
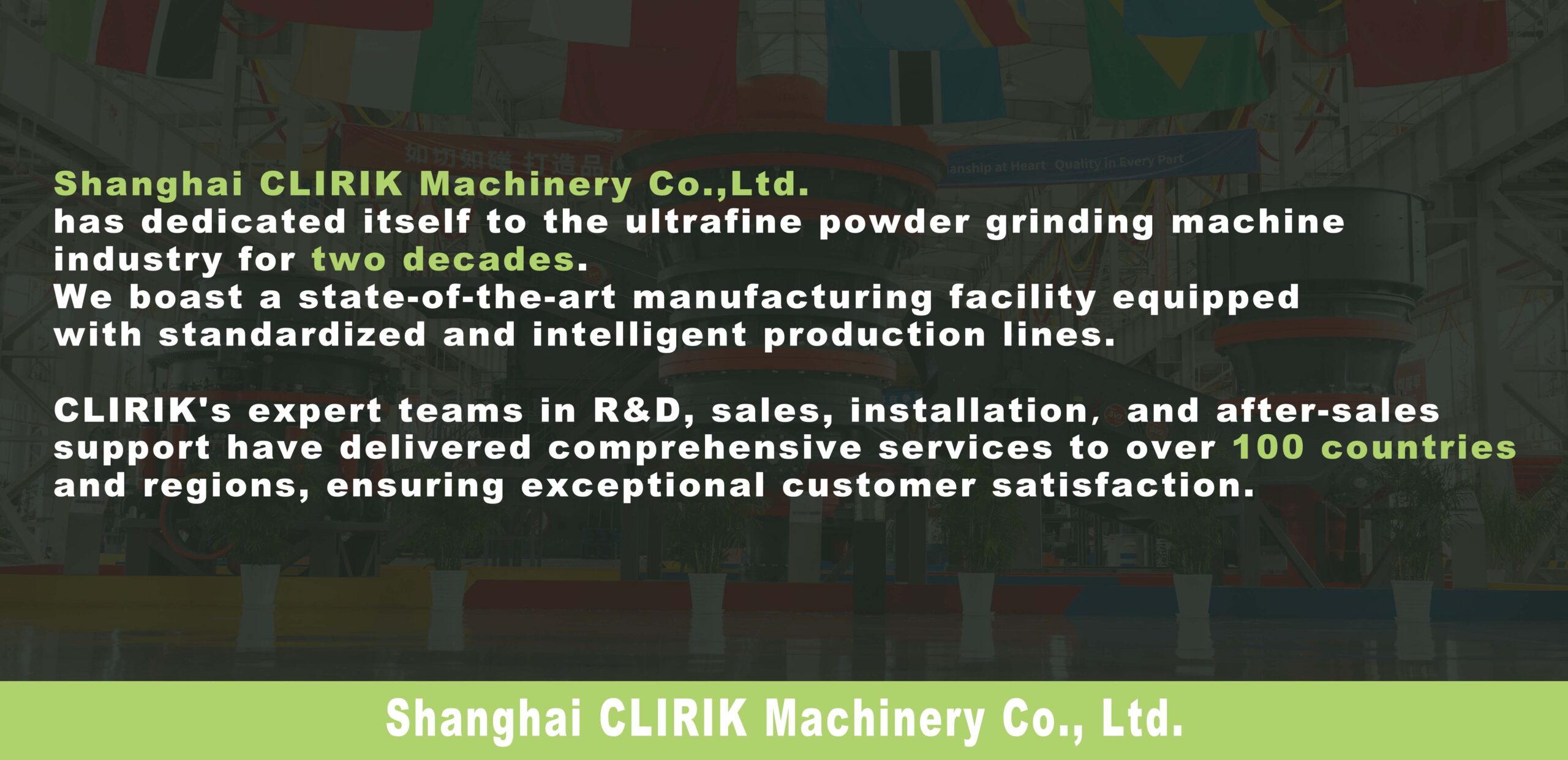
Contact Us Now
Whatsapp:+86 180 0164 2498
Alibaba Store: https://saico.en.alibaba.com/
Equipment Video:https://www.tiktok.com/@clirik.ivy