Raymond mill and ball mill are both commonly used grinding equipment in the powder industry, but there are differences between the two in terms of structure, working principle, scope of application, finished product particle size, output, energy consumption, investment cost, etc. When choosing, users should comprehensively consider the following factors based on the actual processing conditions:
Raymond mill and ball mill are both commonly used grinding equipment in the powder industry. Both have the functions of crushing, grinding, and classification, but they have different limitations in structure, principle, application scope, output, fineness, energy consumption, and floor space. There are some differences in terms of area etc.
★ Structure
Raymond mill is mainly composed of main engine, analytical machine, piping device, blower, finished product cyclone separator, jaw crusher, bucket elevator, electromagnetic vibration feeder, electronically controlled motor, etc. Among them, the main machine consists of a frame, an air inlet volute, a blade, a grinding roller, a grinding ring, a cover and a motor.
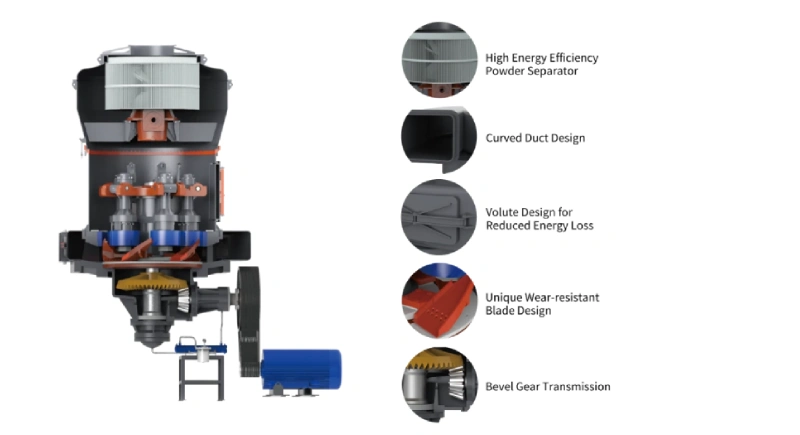
The ball mill is composed of a cylinder, a lining plate, a grinding body, a feeding device, a discharging device, a transmission device, etc. The cylinder is a horizontal cylinder with a lining plate on the inner wall and a grinding body inside the cylinder.
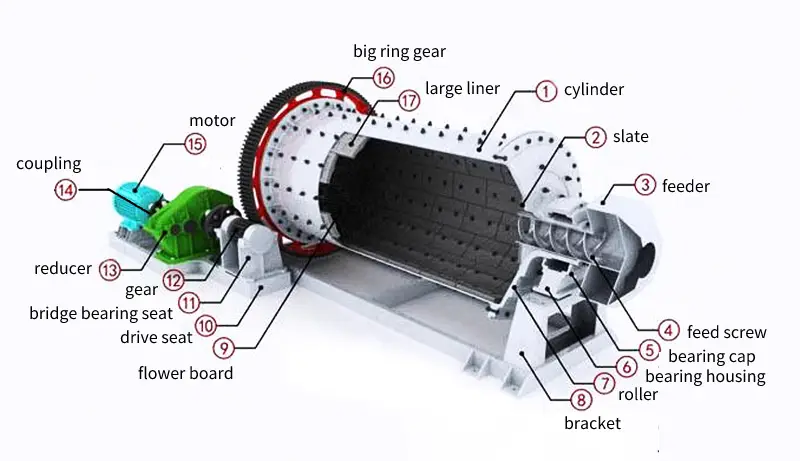
★ Principle
The working principle of Raymond mill is: the material enters the grinding chamber through the feed port and is crushed under the grinding of the grinding roller and the grinding ring. The crushed materials are blown up by the wind and enter the analysis machine for classification. Qualified fine powder is collected by the cyclone separator, while the coarse powder falls back into the grinding chamber to continue crushing.
The working principle of the ball mill is: the material enters the cylinder through the feeding device and is crushed under the rotation of the cylinder and the rolling of the grinding body. The crushed materials are discharged through the discharging device.
★ Application scope
Raymond mill is mainly used to process non-flammable and explosive ores with Mohs hardness not exceeding 9.3 and moisture content not exceeding 6%, such as marble, calcite, limestone, potassium feldspar, etc.
The application range of ball mills is also very wide. It is mainly used in the processing of ferrous and non-ferrous metals with Mohs hardness below level 7 and humidity not exceeding 6%, as well as fertilizers and refractory materials.
★ Yield
The output of Raymond mill is generally smaller than that of ball mill.
★ Fineness
The fineness of the finished product of the Raymond mill can reach 80-325 mesh, while the fineness of the finished product of the ball mill is generally between 20-200 mesh.
★ Energy consumption
The energy consumption of Raymond mill is generally lower than that of ball mill.
★ Covered area
Raymond mills generally occupy a smaller area than ball mills.
Raymond mill and ball mill each have their own advantages and disadvantages, and users should make comprehensive considerations based on actual needs when choosing. Here are some suggestions for selection:
- If the hardness of the material is low and the fineness of the finished product is high, you can choose a Raymond mill.
- If the hardness of the material is high and the fineness of the finished product is not high, a ball mill can be selected.
- If high output is required, a ball mill can be selected.
- If you need to save energy, you can choose a Raymond mill.
- If you need to save floor space, you can choose a Raymond mill.
Specifically, please refer to the following table:
Factors | Raymond Mill | Ball Mill |
Applicable material hardness | ≤9.3 | ≤7 |
Finished product fineness | 80-325 mesh | 20-200 mesh |
Output | Smaller | Larger |
Energy consumption | Lower | Higher |
Floor space | Smaller | Larger |
Price | Higher | Lower |
Additionally, users should consider the following factors:
- Equipment investment and operating costs
- Equipment maintenance and repair costs
- Equipment environmental performance
- Equipment production process requirements