HGM series ultra-fine powder mill
It can be adjusted arbitrarily to produce finished powder with fineness ranging from 150 mesh to 3000 mesh.
Suitable for grinding hundreds of materials with Mohs hardness below level 6.
The equipment investment is small, the operation is simple, and it can operate continuously for 24 hours.
Input size:
≤20mm
Discharging size:
325-2500mesh
Capacity:
0.5-45t/h
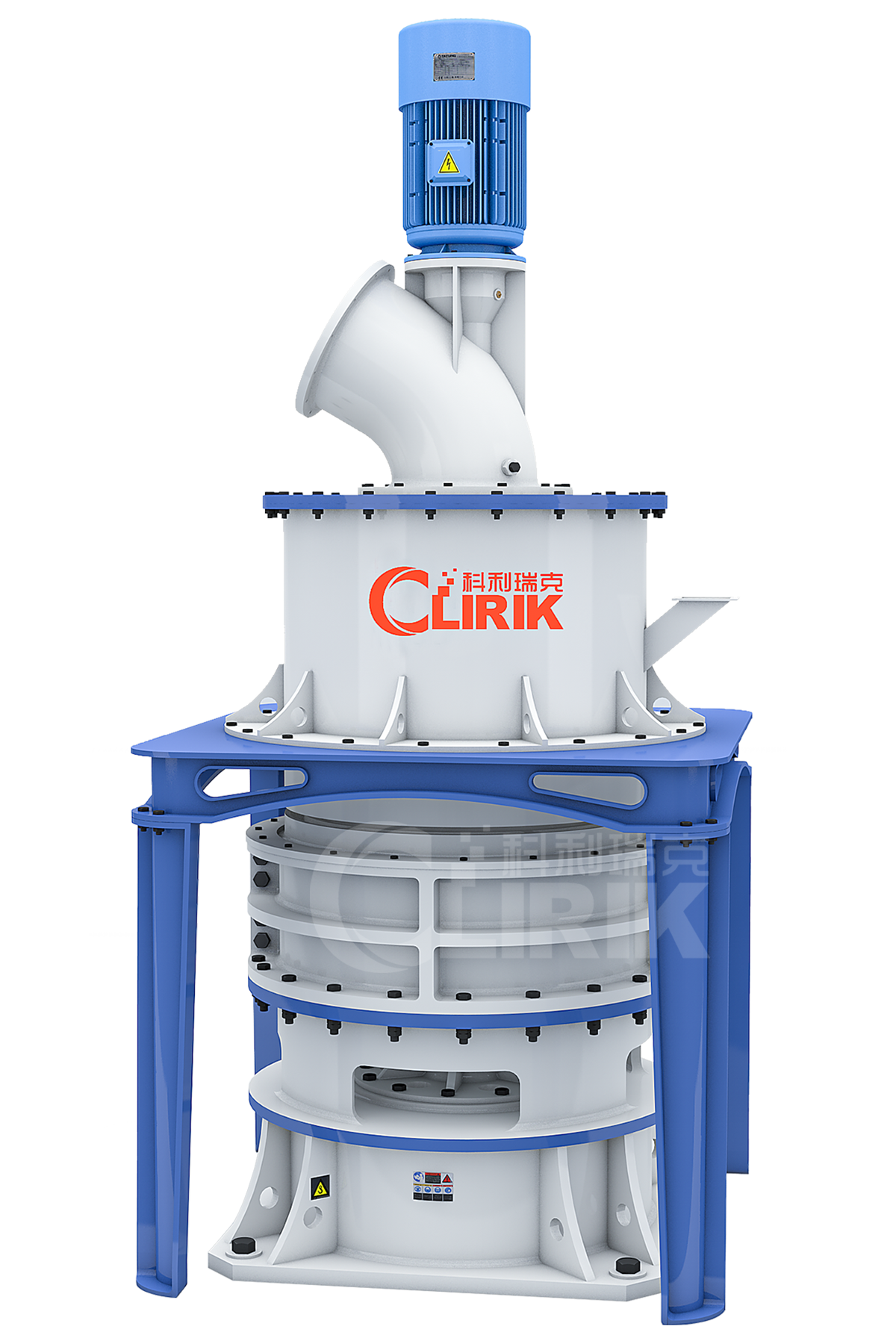
Brief introduction
HGM series ultra-fine grinding mill (three-ring and four-ring medium-speed micro-powder mill) is a professional equipment for processing and manufacturing fine powder and ultra-fine powder.
It has strong technical and cost advantages in the field of mechanical ultra-fine grinding, and has successfully replaced the complex procedures of traditional airflow mill and ball mill grinding and powder selection. It greatly reduces production costs and improves product fineness, and has become an excellent mechanical grinding equipment in the field of fine powder and ultra-fine powder processing.
Thousands of domestic users have proven that HGM ultrafine powder mill has the advantages of superior performance, stable quality, simple operation and convenient maintenance, and is an ideal equipment for ultrafine powder processing.
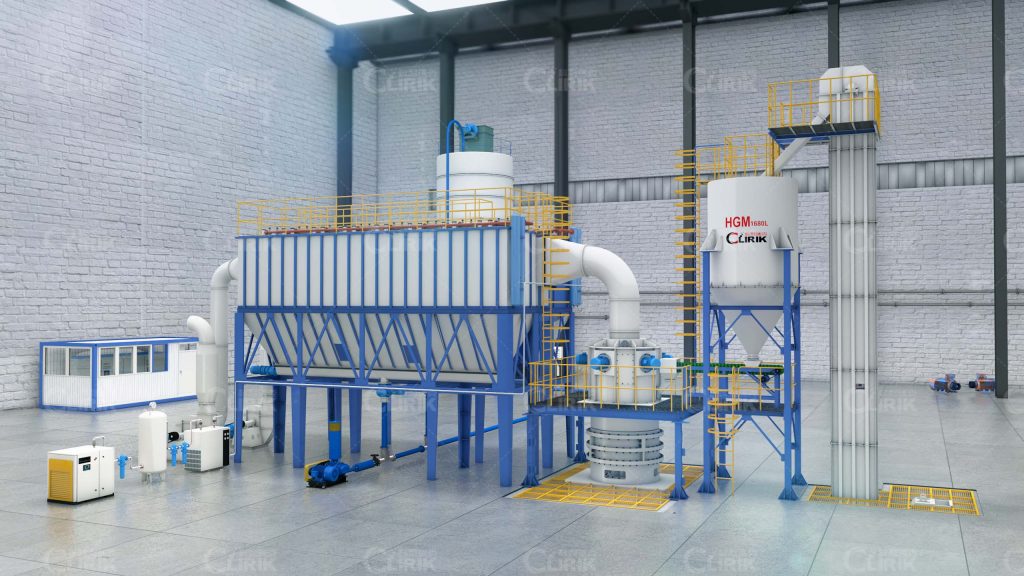
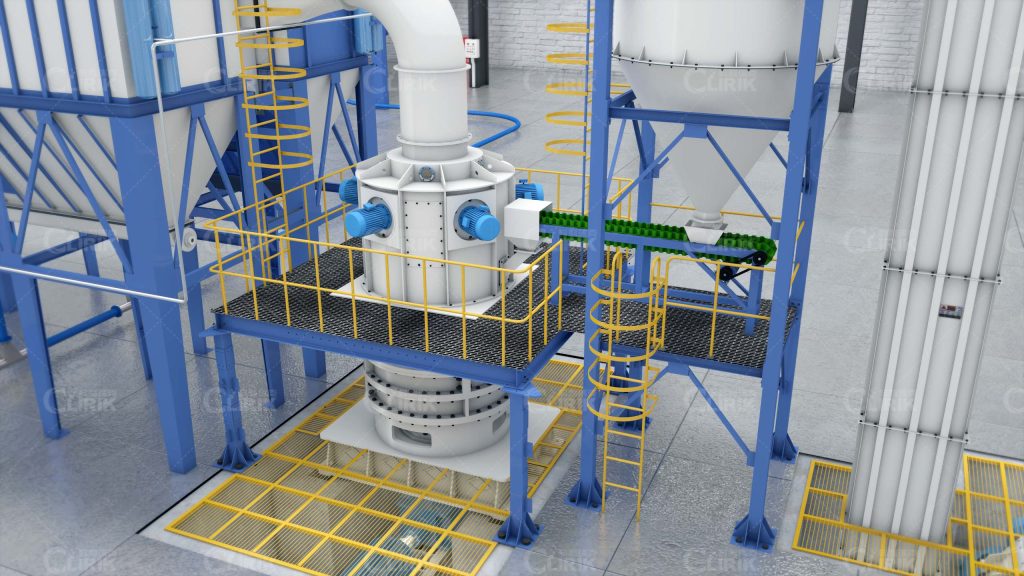
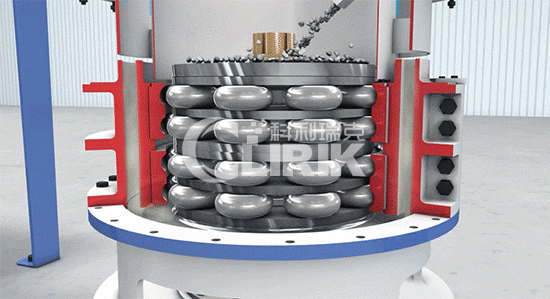
Application Fields
This model is suitable for processing non-flammable and brittle materials with medium and low hardness. It can grind and process calcium carbonate, kaolin, bentonite, talc, mica, attapulgite, barite, gypsum, graphite and many other materials. Its applications have been spread across many industries such as paint, papermaking, pigments, rubber, plastics, fillers, cosmetics, chemicals, etc.
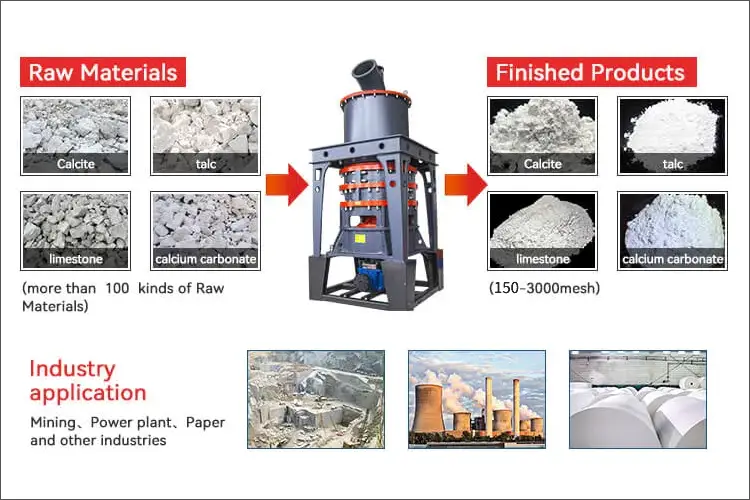
Composition
The standard configuration of HGM ultrafine mill includes main machine, powder separator, diffusion double cyclone powder collector, pulse bag dust collector, high-pressure fan, motor, pipeline and muffler. Optional equipment includes hammer crusher, elevator and feeder, electrical control cabinet.
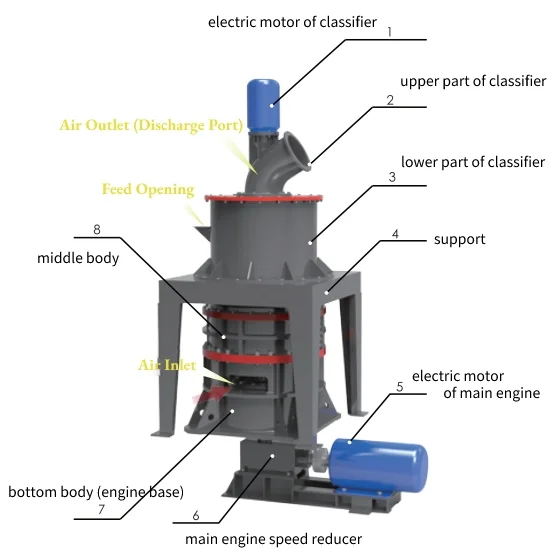
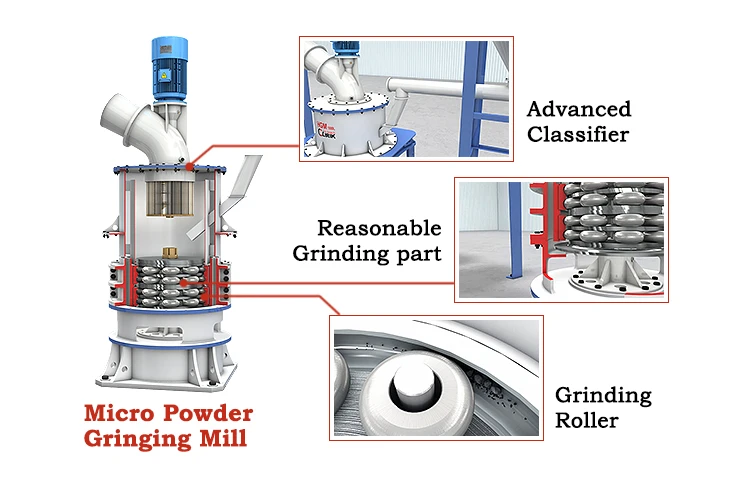
Working Principle
The host motor inputs power to the main shaft through the host reducer to drive the turntables on each layer to rotate. The turntable drives the three-layer ring roller (some models have four-layer ring roller) through the pillar pin to roll in the grinding ring raceway.
The large pieces of material are broken into small particles by the hammer crusher and then sent to the storage bin by the elevator. The electromagnetic vibrating feeder evenly sends the materials to the middle of the upper turntable through the feed port.
The materials will be opened to the edge of the circle under the action of centrifugal force and fall into the ring of the grinding ring, where they will be stamped, rolled and ground by the rollers. The materials will be crushed in the first layer and then fall into the second and third layers for further crushing.
The high-pressure centrifugal fan sucks external air into the machine cavity and sends the materials after three layers of crushing into the powder separator.
The rotating turbine in the powder classifier makes the coarse particles that do not meet the requirements fall back to grinding, while the fine powder that meets the requirements enters the cyclone powder collector with the airflow and is discharged through the discharge valve at the bottom, which is the finished product.
The airflow with a small amount of fine dust is purified by the pulse dust collector and then discharged through the fan and muffler.
Advantages
Under the same finished final size and the same motor power, the capacity of micro powder grinding mill is twice as much as jet mill, mixing grinder and ball mill, and energy consumption decreased 30%.
The ring and roller are forged by special material with high utilization. Under the same grinding material and finish special size, the lifecycle of spare parts is about one year, which is 2-3 times longer than impact mill or turbo mill. Furthermore, the lifetime can reach 2-5 years for grinding calcite carbonate. The lifecycle of spare parts is variable for the material’s hardness.
As no rolling bearings or screws in grinding cavity, there are no problems caused by bolts shedding or rapid wear of bearings and seal components.
The final fineness of the grinding materials can be adjusted between 200 meshes and 2500 mesh.
The application of pulse bag filter and muffler greatly alleviates dust pollution and noise.
Let the material feed into the machine evently, adjust the main speed to fit for grinded materials, the fineness more stable. So as to increase the capacity and efficiency, reduce the power consumption.
Main Specification
Model | HGM80 | HGM90L | HGM100L-Ⅱ | HGM100P | HGM125L | HGM1680L |
Ring Diameter(mm) | 800 | 900 | 1000 | 1000 | 1250 | 1680 |
Ring Number (layer) | 3 | 3-4 | 4 | 4 | 4 | 4 |
Roller Number (PCS) | 18-21 | 24-29 | 28-36 | 28-36 | 30-40 | 30-44 |
Main Shaft Speed (r.p.m) | 230-240 | 200-220 | 180-200 | 180-200 | 135-155 | 120-130 |
Input Size (mm) | ≤20 | ≤20 | ≤20 | ≤20 | ≤20 | ≤20 |
Finished Size (mesh) | 200-2500 | 200-2500 | 200-2500 | 200-2500 | 150-2000 | 150-1500 |
Capacity (t/h) | 0.5-5.5 | 0.8-6.5 | 1.2-10 | 1.2-11 | 2.5-20 | 5-45 |
Overall dimension (L*W*H, m) | 15.1*4.2*7.3 | 18.4*3.9*7.8 | 22.7*3.6*8.5 | 22.7*3.6*8.5 | 27.3*4.2*9.9 | 31.7*7.7*12.6 |
Power Parameters
Model/powder(kw) | HGM80 | HGM90L | HGM100L-Ⅱ | HGM100P | HGM125L | HGM1680L |
Main unit | 75 | 45*2 | 132 | 75*2 | 185-200 | 315 |
Classifier | 18.5 | 18.5-30 | 30 | 37 | 75 | 132 |
Blower | 45 | 55 | 75 | 75 | 110 | 200-220 |
Crusher | 18.5 | 18.5 | 18.5 | 18.5 | 45 | 45 |
Bucket elevator | 3 | 3 | 4 | 4 | 4 | 7.5 |
Feeder | 1.5 | 1.5 | 1.5 | 1.5 | 1.5 | 2.2 |
Discharging valve | 0.75*2 | 1.1 | 1.1 | 1.1 | 1.5 | 1.5*2 |
Air compressor | 11 | 15 | 22 | 22 | 37 | 55 |
Composition of HGM ultrafine grinding production line
The standard configuration of HGM Micro Powder Grinding Mill includes main machine, powder separator, diffusion double cyclone powder collector, pulse bag dust collector, high-pressure fan, motor, pipeline and muffler. Optional equipment includes hammer crusher, elevator and feeder, electrical control cabinet.
Highly automated and good overall benefits
The entire production line is highly automated, with high grinding efficiency, more stable operation, reduced maintenance intensity and production costs, high quality finished products, and good overall benefits.
Adapt measures to local conditions and optimize solutions
The production line construction plan is designed by CLIRIK’s professional team based on field examination data and customer production needs, and the production operation process is smooth.
Integrated design, low comprehensive investment
The line integrates processes from crushing to transportation, with a compact layout occupying about half the space of a traditional ball mill system. It’s designed for outdoor setup, minimizing initial investment and equipment costs.
High environmental standards and more automation
The equipment operates stably and vibrates little, so the noise is low. The system is fully sealed and works under negative pressure, with no dust spillage, a clean environment, and emission standards far exceeding international standards. It is equipped with an expert automatic control system, which can realize free switching between remote control and local control. It is easy to operate and saves labor.
What is the difference between HGM micro powder mill and ball mill?
Micro-powder mill and ball mill are both grinding equipment, but they have certain differences in working principles, applicable materials, finished product fineness, production capacity, energy consumption, etc. Some customers who don’t know much about these two devices may not know how to make the right choice. Below is a simple comparison of the two devices to help you choose a more suitable grinding device.
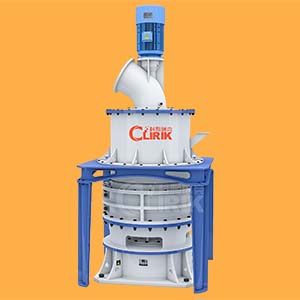
The discharge fineness of the micro-powder mill can reach 2500 mesh, which is suitable for crushing materials with higher fineness requirements, such as talc, limestone, kaolin, etc.
Adopting “grinding roller-grinding ring” rolling grinding method
The powder has less impurities, high whiteness, and slightly worse sphericity than the ball mill
High grinding efficiency, Low energy consumption
Small production capacity, wide fineness range, high 2μm fine powder content
Efficient and flexible control of product categories, enabling conversion of different raw materials on one machine in a short time
VS
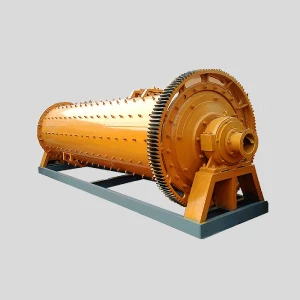
The discharge fineness of the ball mill is generally between 20 and 200 mesh, and it is suitable for crushing materials with lower fineness requirements, such as iron ore, coal, etc.
Utilize grinding media and adopt “ball-cylinder” impact grinding method
The purity of the powder is lower than that of micro powder mill, with lower whiteness and better sphericity
Low grinding efficiency, High energy consumption
Large production capacity, narrow fineness range, low proportion of fine powder
Producing a single product requires a long cleaning time