Shanghai Clirik Machinery Leads the Way in Mineral Grinding Innovation
Amidst the rising global demand for high-grade gypsum products in diverse sectors such as construction, healthcare, and agriculture, Shanghai Clirik Machinery has introduced its HGM Grinding Mill, a groundbreaking solution that optimizes the processing of gypsum ore with cutting-edge engineering and sustainable practices.
The Versatile Role of Gypsum Ore in Modern Industries
Gypsum (CaSO₄·2H₂O), a soft sulfate mineral known for its fire-resistant and binding properties, is a fundamental material in modern infrastructure development. Its applications are widespread:
With a Moh‘s hardness of 2 and a layered crystalline structure, raw gypsum needs precise grinding to achieve functional particle sizes ranging from 80 to 600 mesh. Traditional grinding mills often face challenges such as energy waste and inconsistent fineness, which the HGM series from Clirik effectively addresses.
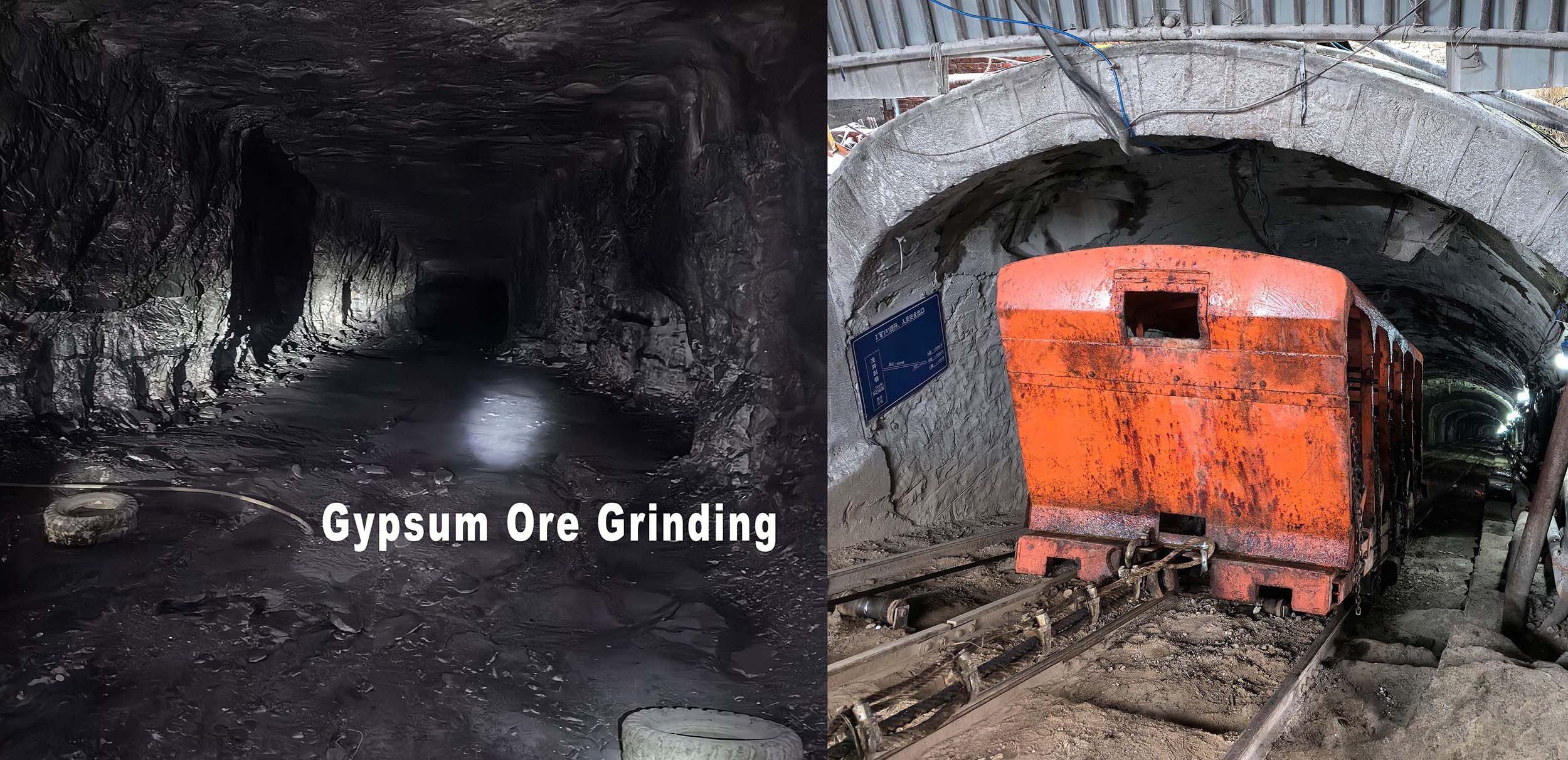
HGM Grinding Mill: Unmatched Engineering and Performance
Combining German manufacturing standards with proprietary innovations, Clirik’s HGM series delivers superior performance:
Key Technical Specifications
Core Advantages
Triple Grinding Zones
– Hammer crushing, roller compaction, and ring abrasion ensure progressive size reduction.
Intelligent Classification
– Turbine classifiers achieve 99.9% screening accuracy through AI-driven speed modulation.
Eco-Friendly Design
– Pulse dust collectors maintain emission levels below 10mg/m³, exceeding EU standards.
Low Maintenance
– Modular assembly allows roller replacement within 4 hours, compared to 2 days for conventional mills.
Operational Workflow
Why Global Producers Prefer the HGM Mill
“After replacing our Raymond mill with Clirik’s HGM128 model, our gypsum powder whiteness increased from 85% to 92%, while energy costs dropped by 40%,” said Zhang Wei, plant manager at Gypsum Co. Ltd. “The automated PLC system also reduced labor needs by 60%.”
Clirik’s R&D team has further enhanced the mill with gypsum-specific configurations:
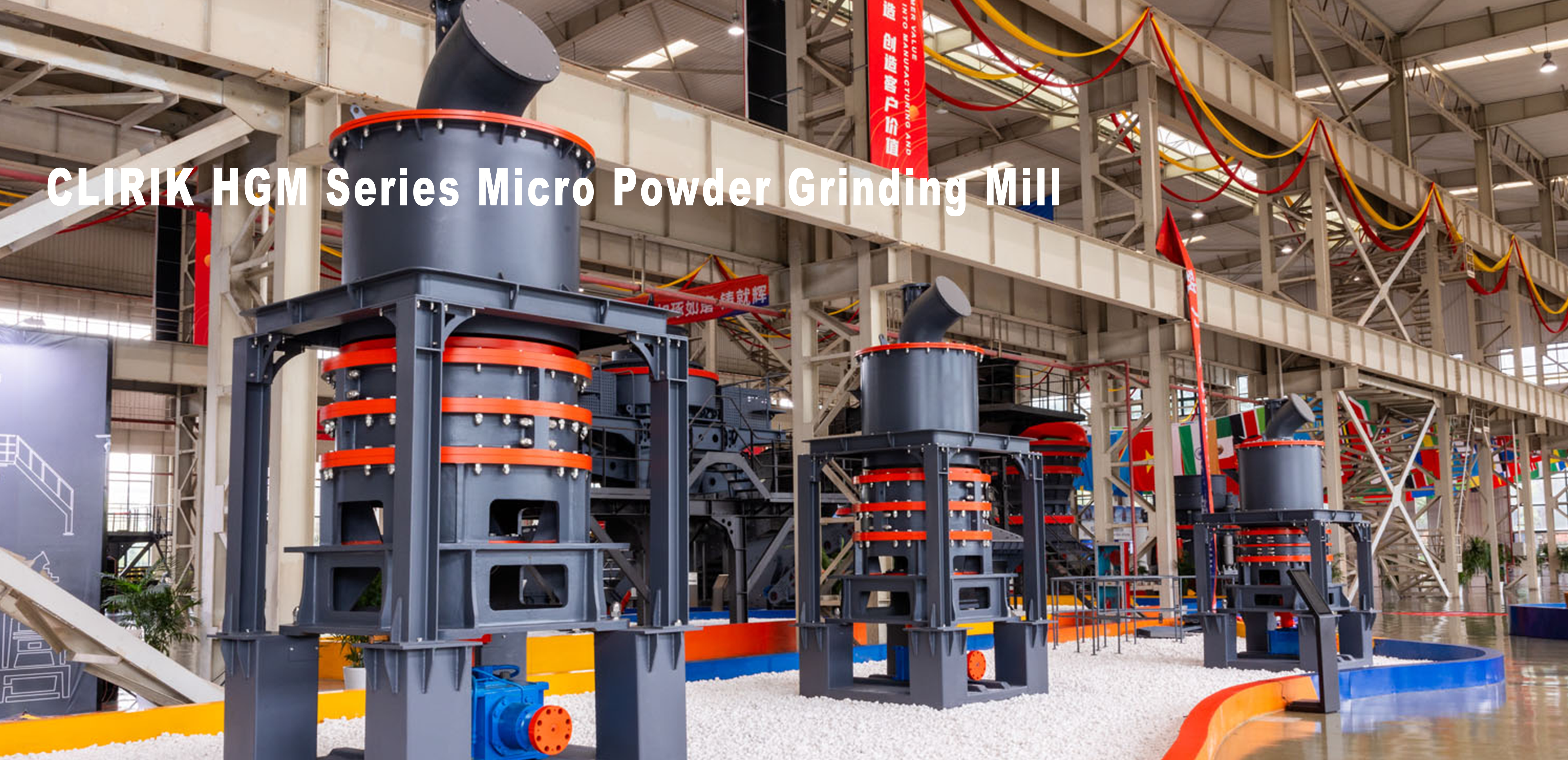
Commitment to Sustainability
By reducing power consumption to 18-22 kWh/t (compared to the industry average of 35 kWh/t), each HGM mill prevents 450 tons of CO₂ emissions annually, equivalent to planting 20,000 trees.
Availability and Customization
Clirik offers free material testing and 24/7 technical support through its global network. The HGM series is available in 5 models with capacities ranging from 0.5t/h to 45t/h, suitable for processing natural gypsum, FGD gypsum, and phosphogypsum.